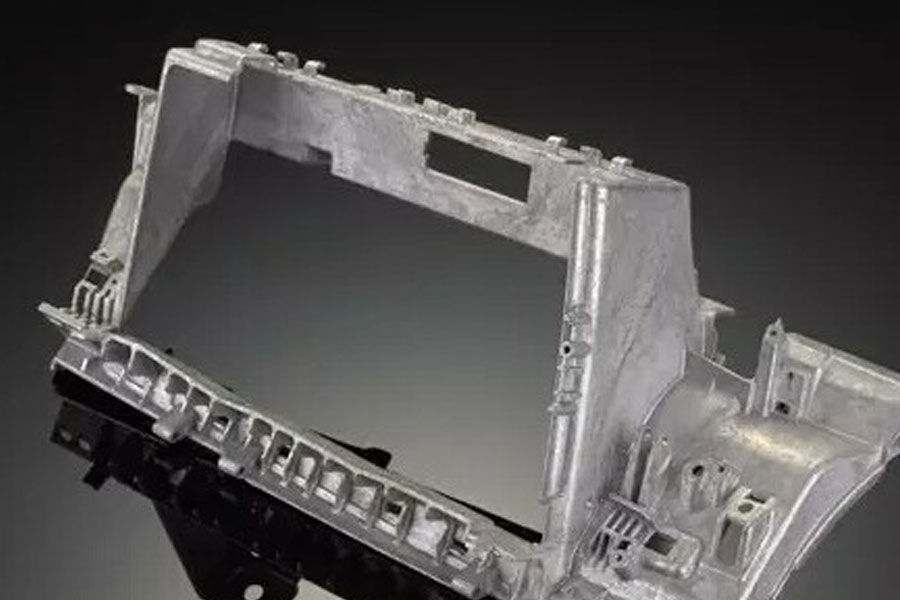
鋳造成形法は、生産効率が高く、低コストで、より複雑な形状の製品を生産できるため、液体充填性に優れ、マグネシウム合金の成形法の中で支配的な地位を占めている。しかし、鋳造マグネシウム合金の製造工程に起因して、組織の密度が十分でなく、引け巣や引け巣などの欠陥が多く、機械的性質が悪い。押出、鍛造、圧延などの塑性加工工程を経て製造されたマグネシウム合金製品は、組織が緻密であり、機械的性質が良好である。押し出し、鍛造、圧延などの塑性加工によって製造されたマグネシウム合金製品は、組織が緻密で、マグネシウム合金製品の機械的特性を向上させることができる。現在、効率的で低コストのマグネシウム合金塑性加工法がないため、マグネシウム合金塑性加工の応用は限られている。したがって、高効率で低コストのマグネシウム合金塑性加工法の開発は、高強度マグネシウム合金の大規模な応用を促進する唯一の方法となっている。マグネシウム合金には主に以下の塑性加工技術がある:
Forged
マグネシウム合金の鍛造工程はより複雑である。鍛造工程では、局部的な変形が不均一になりやすいため、ワークの特性や組織も不均一になります。鍛造用マグネシウム合金としては、Mg-Zn-Zr系とMg-Al-Zn系がよく使われる。高温での材料の強度に対する要求が高い場合、WEシリーズに希土類元素を添加したマグネシウム合金の強度は容易に要求を満たすことができる。鍛造工程では、変形の程度、最終鍛造温度、変形の仕方がマグネシウム合金鍛造品の機械的性質に影響する主な要因である。現在、主にパンチ鍛造、等温鍛造、温間精密鍛造などの成形技術を開発した。
押出成形
押出成形は、成形すべき金属ブランクを密閉された押出シリンダー内に配置し、ブランクに一定の圧力を加えて押出ダイ内で材料を変形させる塑性加工法である。成形中、金属ブランクは三次元圧縮応力状態にあるため、成形法では金属ブランクの塑性を十分に発揮させることができる。押出製品は、良好な表面品質、高い寸法精度、およびコンパクトな構造を有する。そのため、マグネシウム合金押出製品は、自動車、航空宇宙、電子分野で大きな需要がある。一般的に、マグネシウム合金の押出成形は熱間押出成形と温間押出成形に分けられ、使用される設備は基本的に他の金属材料と同じである。
ロールフォーミング
マグネシウム合金板は、そのユニークな利点により、航空宇宙および自動車3C産業において幅広い用途が見込まれている。現在使用されているマグネシウム合金板のほとんどは圧延によって成形されている。しかし、マグネシウム合金板の圧延成形工程はより複雑で、通常3パス以上の熱間圧延を必要とする。マグネシウム合金板の圧延は次のような特徴がある:歩留まりが低い、生産効率が低い、利益が大きい、品種が比較的単一である。
プレス・成形
マグネシウム合金のプレス加工は他の材料とは異なる。マグネシウム合金は室温での塑性が低い。従来の冷間プレス成形はマグネシウム合金には適していません。マグネシウム合金のホットスタンピング成形を行うには、通常150℃以上に加熱する必要がある。現在、マグネシウム合金のホットスタンピングはある程度研究されていますが、その重要な問題は十分に解決されておらず、マグネシウム合金板の工業への幅広い応用をある程度妨げています。
ドロー成形
マグネシウム合金の絞り成形の過程では、材料は引張と圧縮の両方向の応力がかかった状態にある。この時、材料の塑性は発揮されにくい。従って、マグネシウム合金の成形には引抜は適さない。伸線加工された製品は、表面粗さが高く、寸法精度が良いという特徴がある。線材やパイプは、伸線加工と成形加工によって製造されるが、これは生産効率が高く、高速連続生産が実現しやすい。また、伸線によって形成されたマグネシウム合金線の強度はより高い。
超塑性成形
超塑性成形は、複雑な形状や大きな変形を伴う加工に使用できる。これは、特定の条件下で一般的な塑性指数を超える金属特性である。従って、超塑性成形は塑性の乏しいマグネシウム合金製品の加工に利用できる。しかし、マグネシウム合金の超塑性成形に関する研究は始まったばかりであるため、問題点も多い。マグネシウム合金の超塑性変形メカニズムについてコンセンサスを得ることは難しい。マグネシウム合金の超塑性成形はさらなる研究が必要である。