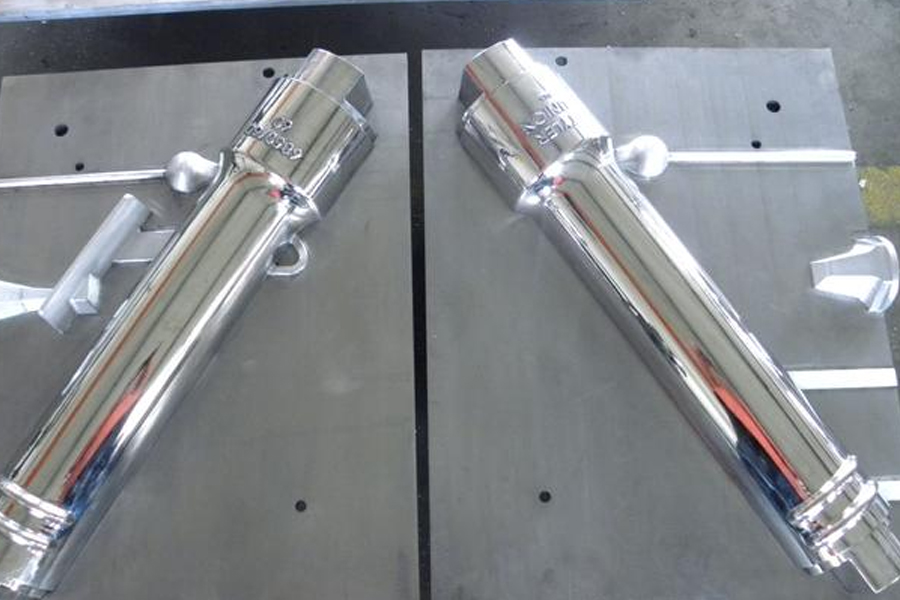
重力金型鋳造に比べ、低圧鋳造は加圧下での充填と結晶凝固により、成形品質が良く、工程歩留まりが高いという利点があるが、複雑な形状や高い性能が要求されるシリンダーヘッド鋳造では、複雑な工程があり、制御には高度な技術的困難が要求される。そこで本稿では、アルミ合金シリンダーヘッドの低圧鋳造技術とパラメータ制御のポイントに焦点を当て、低圧鋳造プロセスの技術的優位性を最大限に発揮し、高品質のシリンダーヘッド鋳造品を生産することを目的とする。
シリンダーヘッドの低圧鋳造工程のポイント
2.1 ゲーティング・システムの例
シリンダーヘッドの低圧鋳造工程計画は、一般に、ライザーパイプと複数のゲートを有する形態であり、これは多重分割の一形態である。例えば、4気筒シリンダーヘッドの場合、代表的なゲート方式は2つあり、すなわち燃焼室側に2つまたは4つのゲートが設置されている。図2は2ゲートの工程概略図である。この方式は、1つの金型または2つの金型に適している。
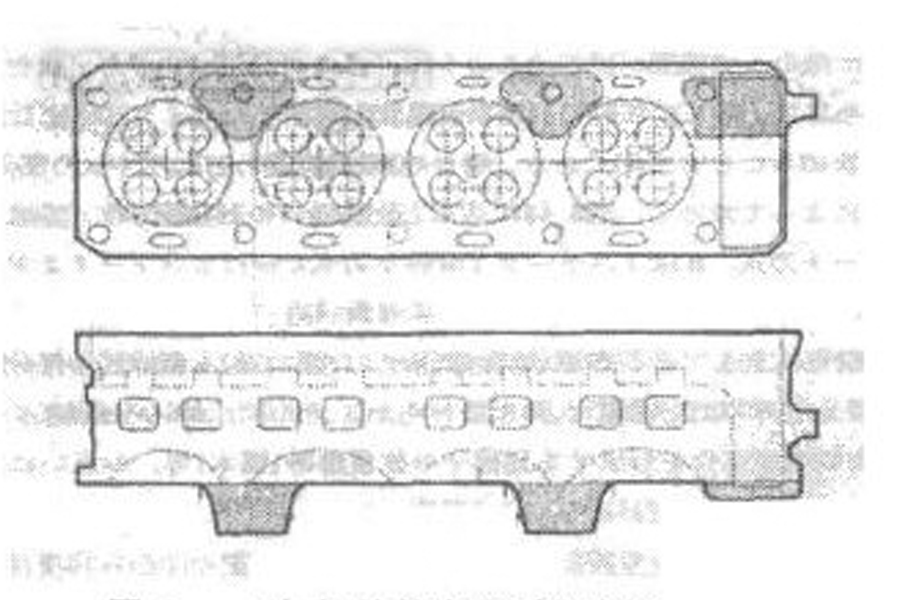
2.2 合金材料と溶解
アルミニウム合金シリンダーヘッドの材料は、一般的にZL105や107などのAI-Si-Cu系合金を選択します。伸びと耐食性が要求される場合は、ZL101とZL104も使用できる。高品質の溶湯を得るためには、Arガス回転吹錬を行い、Srを添加して改質し、AJ-Ti-Bを添加して結晶粒を微細化するのが標準的な操作である。
2.3 注入工程
2.3.1 金型のメンテナンス
高品質のシリンダーヘッド鋳物を安定して生産し、金型の寿命を延ばすためには、金型の定期的な清掃とメンテナンスが非常に重要です。一般的に、金型のメンテナンスは500~700個生産するごとに行う必要があります。主な内容は、金型を分解し、キャビティの表面コーティングを柔らかいブラシで清掃し、エジェクタロッドと排気孔の隙間に入り込んだアルミ片やコーティング粒子を除去することです。鋳造形状、スムーズな排出、スムーズな排気の品質を確保する。
2.3. 2 コーティング
流し込む前に型を200℃程度に予熱し、塗料を吹き付ける。シリンダーヘッドの形状は複雑であるため、部品によって塗料の厚さが異なることに特に注意を払う必要がある。一般的な部品の塗装厚さは0.1~0.2mmで管理される。例えば、燃焼室の表面は、O.OSmnの厚さで細かい粒子をコーティングする必要があります。ゲート、ライザー、インナー・ランナーなど、ゆっくりと固化させる必要がある場所には、より厚くすることができ、一般的には約0.5~1mmです。
2.3.3 フィルター
フィルターを設置する目的は、ライザー管内の酸化不純物が空洞に入るのを防ぎ、層状充填を形成することです。安価で効果的な亜鉛メッキメタルメッシュを使用することができます。4--0.6mm、1214メッシュ。
2.3.4 温度
アルミ溶湯の温度はシリンダーヘッドの内部欠陥や外観品質に大きな影響を与える。注湯温度は680~730℃の範囲とし、実操業での温度偏差は20℃以内に管理する。
低圧鋳造の特徴は、良好な順次凝固を得ることである。この後、低圧鋳造ではレポート温度を適度にコントロールすることが重要である。理想的な鋳型温度分布は、ゲートから上型にかけて徐々に低下させ、各部位の比表面制御範囲を変更して得る。シリンダーヘッド鋳物の性能向上と生産サイクル短縮のためには、上型と側型に上記の温度領域と冷却を徹底する必要がある。一般的に水冷と空冷に分けられ、多チャンネル設定を使用し、各チャンネルは独立して自動制御されます(流量と圧力)。水冷は圧送水ポンプを採用し、金型内部の高温気化による水流不良の問題を解決し、空冷は圧縮空気を使用する。
シリンダーヘッドには複数のゲートがあるため、2つのゲート間の距離が短いとゲート間の鋳造部の温度が上昇し、ゲートとこの部分の凝固順序が逆になる。そのため、必要な温度勾配を得るためには、この部分に局所的な強制冷却を設定する必要がある。
鋳型の寿命と安全性を考慮すると、間接冷却を主な冷却方法とすべきであり、局部鋳造品の厚みが大きい場合には直接冷却を使用することができる。冷却強度には、時間制御と温度制御の2つの方法がある。時間制御は、水または空気の通過時間を制御することである。この方法は単純で実施しやすいが、精度は高くない。温度制御は、冷却位置に熱電対を設置し、熱電対で測定された温度に応じてパソコンが冷却水または空気をオン・オフする方法である。制御精度は比較的高い。
近年、凝固数値シミュレーション技術の発展は、シリンダーヘッドの低圧鋳造工程の最適化に良い参考となる。異なる条件下での凝固試験結果を十分に把握し、鋳造工程の管理を強化し、鋳造品の品質を確保することができます。
2.3.5 加圧時間
ゲートの充填から固化までの時間をプレスタイムと呼び、温度に大きく影響される。安定した生産条件下では、シリンダーヘッドの重量によって加圧時間は異なるものの、概ね2~8分に抑えられている。生産効率向上の観点から、1金型、2部品、2段加圧などの方法で時間短縮を図ることができる。
2.3. 6 離型時間
加圧時間と同様、温度変化によって変化する。加圧時間が短いと鋳物が変形しやすく、長すぎると鋳物が金型にはまり込んで取り出せなくなる。そのため、加圧時間の1/3程度に制御するのが一般的である。また、鋳物の冷却速度を上げるため、鋳型の引き抜き時に離型抵抗の小さい側型を先に開き、一定時間冷却した後に上型を開く方法もある。
2.3. 7 圧力曲線
加圧圧力は流体充填性能と溶湯の供給効果に直接影響し、加圧曲線は低圧鋳造プロセス制御の重要な部分です。加圧圧力は以下の式で計算できます:
P=γx(1+S/A) x ΔH x 10-2
上式中、P-圧力(MPa)、γ-アルミ液比重(2.4〜2.5)、ΔH-アルミ液上昇高さ(m)、S-リフトパイプ断面積(m2)、A-キャビティ断面積(m2)o
押し湯の供給圧力は一般的に0.005~0.01MPa程度です。高圧の効果は良いのですが、圧力が0.01Mpaを超えると、塗膜の剥離やアルミ液が鋳型のベントを塞いだり、砂中子内に侵入したりします。砂中子の燃焼によって発生するガスを注湯中に時間内に排出することは非常に必要なことですが、シリンダーヘッドに使用される砂中子は構造が複雑で数も最大であるため、金型に多数のベントホールを設けることは困難です。このとき、押湯の押湯圧を上限近くまで高めると、鋳造にガスが巻き込まれるのを効果的に防ぐことができる。
シトラスケーブ内の液面の変化は圧力曲線の再現性に影響するため、シトラスケーブ内の圧力を自動的に補正する必要があります。シリンダーヘッド鋳造の場合、圧力曲線のゼロ点I81を正確に制御するためにセンサーを設定することができます。
また、ライザーパイプの下端からオレンジポットの底までの間隔が短すぎると、溶液に乱流が生じやすくなります。したがって、溶液の使用に影響を与えない範囲で、ライザーパイプの下端とオレンジポットの底部との間隔は200mm程度とする。
鋳造欠陥とその対策
表1に低圧鋳造の一般的な欠陥とその対策を示す。シリンダーヘッドのような複雑な部品では、様々なパラメータの変動が鋳造品質に影響を及ぼす可能性がある。従って、工程計画、型設計、鋳造工程など様々な角度から詳細な分析・調査を行い、欠陥の様々な原因を明らかにし、その上で対策を講じる必要がある。
Conclusion
これまでのところ、アルミ合金シリンダーヘッドは、低圧鋳造に適した数少ない限られた自動車部品の一つである。そのため、生産率が高く、内部品質が良いという利点を十分に発揮し、国内の低圧鋳造技術の生産とアルミ合金シリンダーヘッドの応用を拡大する。我が国の自動車技術の急速な発展に適応する。