1.1 概要
1958年、H.F.シュローヤーは発泡プラスチック模型で金属鋳物を作る技術を発明し、特許を取得した。当初使用された模型は、ポリスチレン(EPS)板をバインダー入りの砂で成形したものだった。ドイツのGrunzweig社とHarrtmann社がこの特許を購入し、開発・応用した。バインダーを含まない乾燥砂を使って鋳物を製造する技術は、その後1964年にT.R.スミスが特許を取得した。1980年以前は、バインダーフリーのドライサンドプロセスの使用は、フルモールドプロセス社(Full Mold Process (Inc) )の承認が必要であった。その後、特許は無効となった。
最も一般的で実用的な方法は、耐火物でコーティングされた模型を砂箱に入れ、乾燥砂で模型をしっかりと充填し、液体金属を注入して発泡模型を置き換えることである。この鋳造法は、ロストフォーム鋳造(EPC)、ガス化鋳型鋳造、固体鋳型鋳造などと呼ばれている。アメリカ鋳造協会のロストフォーム鋳造委員会は、この鋳造法の名称として「ロストフォーム鋳造」を採用した。
ロストフォーム鋳造は、シリンダーブロック、シリンダーヘッド、クランクシャフト、ギアボックス、インテークパイプ、エキゾーストパイプ、ブレーキハブなどの非鉄および鉄金属製パワーシステム部品の製造に使用できる革新的な鋳造プロセスです。ロストフォーム鋳造の工程フローは以下の通りです:
1)予備発泡 模型製作は、ロストフォーム鋳造プロセスの最初のステップである。シリンダーヘッドのような複雑な鋳物の場合、いくつかの発泡模型を別々に作り、それを接着して全体の模型を作る必要があります。各ブロックモデルには、製造用の金型一式が必要です。さらに、各ブロックの正確な位置決めを維持するために、接着作業でも一組の鋳型が必要になる場合があります。モデルの成形工程は、2つのステップに分けられる。最初のステップは ポリスチレンビーズを適切な密度に予備膨張させることである。この段階を予備膨張と呼ぶ。
2) モデル成形 膨張前のビーズをまず安定させ、成形機のホッパーに送り、供給孔から供給する。金型キャビティに予備膨張ビーズを充填した後、蒸気を導入してビーズを軟化させる。ビーズが膨張し、すべての隙間が埋まり、1つのボディに接着され、発泡模型の製造工程が完了します。
成形後、金型の水冷キャビティ内で大量の水流によって金型を冷却し、金型を開いて金型を取り出す。この時、金型の温度が上昇し、強度が低下する。そのため、脱型時や保管時には変形や破損を防ぐために注意が必要である。
3) モデル・クラスターの組み合わせ モデルを使用する前に、適切な期間保管し、モデルを成熟させ、安定させる必要がある。一般的な模型の保管期間は最大30日間である。独自に設計された金型によって形成された模型の場合は、2時間の保管で済む。模型が成熟し安定したら、2つの部分に分けることができる。ブロックモデルは接着される。ブロック模型の接着は、ホットメルト接着剤を使った自動接着機で行われる。接着面の継ぎ目は、鋳造欠陥の可能性を減らすため、しっかりとシールする。
4) 模型クラスター浸漬塗装 1箱により多くの鋳造品を生産するために、多くの模型をクラスターに接着し、模型クラスターを耐火性塗料に浸漬し、約30~60℃(86~140F)の空気循環式オーブンで2~3時間乾燥させた後、乾燥させ、模型クラスターを砂箱に入れ、乾燥砂で満たし、きつく振動させることがある。模型群の内部の空洞と外側の乾燥砂は、すべて圧縮して支えなければならない。
5) 注湯 模型群を砂箱の中で乾燥砂でしっかりと充填した後、鋳型を注湯することができる。鋳型に溶融金属を流し込んだ後(鋳造温度はアルミ鋳物で約760℃/1400F、鋳鉄で約1425℃/2600F)、模型を気化させる。金属を交換して鋳物を形成する。図1は、ロスト・フォーム・プロセスの砂箱と注湯の模式図である。
ロストフォーム鋳造プロセスでは、従来の中空鋳造よりも注湯速度が重要になる。注湯が中断されると、砂型が崩れて無駄が生じる可能性がある。そのため、1回の注湯の差を少なくするためには、自動注湯機を使用するのがベストです。
図1 ロストフォーム工程の砂箱と注湯の模式図 6)落砂清掃 注湯後、鋳物は砂箱の中で凝固・冷却し、砂から落下する。鋳物の落砂は極めて単純で、砂箱をひっくり返すと鋳物は緩い乾燥砂から落下する。その後、鋳物は自動的に分離され、洗浄され、検査され、鋳物箱の中に運び去られる。
乾燥砂は冷却後に再利用でき、その他の追加工程はほとんど使用されない。金属スクラップは再溶解して生産に使用できる。
1.2 ロストフォーム鋳造法の利点
ロストフォーム鋳造法には、技術、経済性、環境保護の3つの面で利点がある。
1. 2. 1 技術的側面
1) 模型設計の自由度向上 新しいプロセスでスタイリング設計を行うことが可能であり、最初の段階から模型にいくつかの機能を追加することも十分に可能である。例えば、ディーゼル・プレヒーターには特殊な機能部品があり、従来の鋳造法の代わりにロストフォーム鋳造法で製造することができる。2) 鋳物の製造に使用される砂中子の廃止
3) 多くの鋳物はライザーなしで供給できる。
4)鋳造精度の向上 複雑な形状や構造を得ることができ、繰り返し100%の再現性で高精度鋳造品を生産することができ、鋳造品の肉厚偏差は-0.15~+0.15mmの間で制御することができます。
5) モデルの接合面にフラッシュがない。
6) 鋳物の重量を約1/3にできる利点がある。
7)加工代の削減 加工代を削減し、一部の部品は加工しないこともできる。これにより、機械加工や工作機械への投資を大幅に削減することができる(例えば、状況に応じて投資を半分に減らすことができる)。
8) 従来のキャビティ鋳造と比較して、金型投資が削減される。9) 完全に落下砂および中子の従来のプロセスを除去して下さい
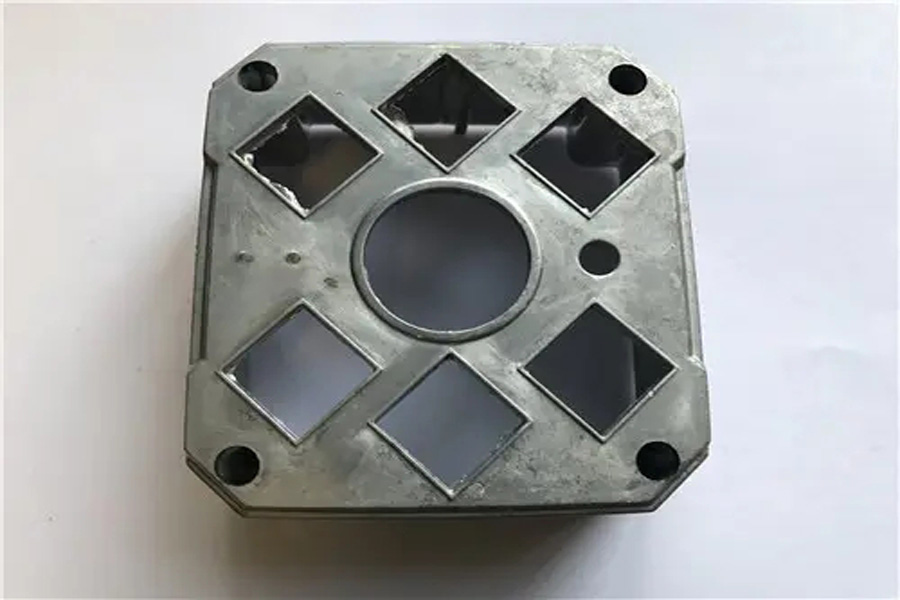
1) それは複雑な鋳造物を全体として作り出すことができます 新しいプロセス設計を採用して、全体的なモデルを形作るためにブロック モデルを接着し、複雑な必要な部品に投げることができます。元の複数の鋳造のアセンブリ部品(ディーゼルの予熱器など)と比較して、それは1〜10倍から利益を得ることができます。
2) 工場の人員削減 ロストフォーム鋳造工場を設立するには、従来の鋳造工場よりも従業員数が少なくなるため、この要素を考慮する必要がある。
3)柔軟な鋳造プロセス 新しいプロセスでは、フラスコ内で多数の類似または異なる鋳物を同時に生産することができるため、鋳造プロセスの柔軟性は非常に重要である。つまり、それぞれの利点は経済的利益に合致し、同時に労働条件の改善にもつながると言える。
1. 2. 3 環境保護
ポリスチレンとPMMAは燃焼時に一酸化炭素、二酸化炭素、水、その他の炭化水素ガスを発生し、その含有量はヨーロッパで認められている基準よりも低い。乾燥砂は、100%リサイクル可能でバインダーを含まない天然珪砂を使用することができる。模型に使用される塗料は、バインダーとその他の副資材を水に加えたもので、公害を引き起こさない。