アルミ・マグネシウム合金は密度が低く、強度が高いため、ますます広く使用されている。その中で、アルミ-マグネシウム合金ダイカスト技術は、先進的な切削加工として、生産効率が高く、原材料を節約し、生産コストを削減し、製品の性能がよく、精度が高いという特徴がある。主に電子、自動車、モーター、家電などの産業で使用され、一部の高性能、高精度、高靭性の高品質アルミ・マグネシウム合金製品は、大型航空機、船舶など比較的技術要求の高い産業にも応用されている。
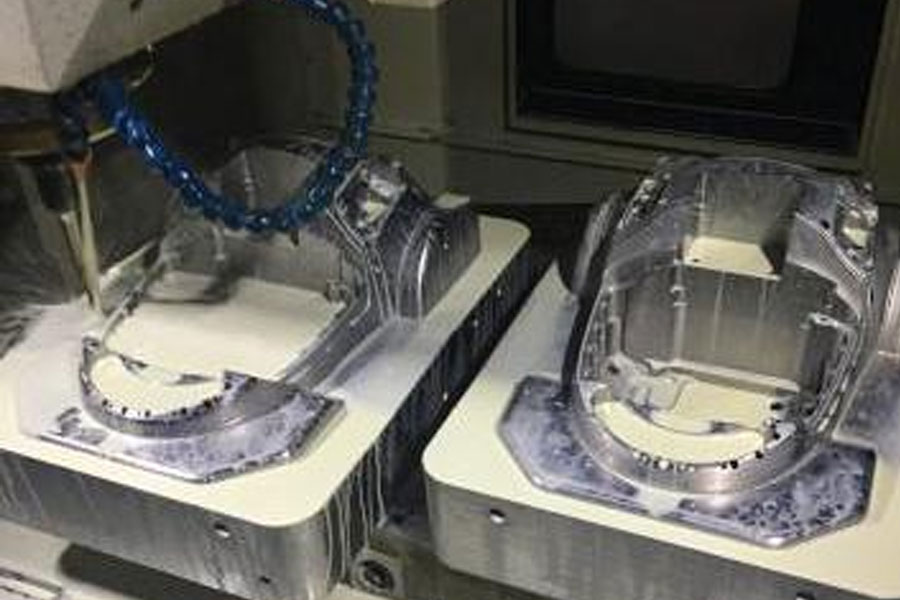
アルミニウム・マグネシウム合金ダイカスト金型の作業条件と性能要件
アルミ・マグネシウム合金ダイカスト金型は、アルミ・マグネシウム合金鋳物をダイカストマシンでダイカストするための金型です。アルミニウム合金の融点は600~750℃、マグネシウム合金の融点は600~700℃です。一般的に加工面温度は500~600℃まで上昇します。キャビティ、マンドレル、ノズルの表面はいずれも温度変化が激しく、金型表面には熱疲労亀裂が発生しやすい。また、アルミ・マグネシウム合金はダイカスト加工時に金型表面に付着しやすく、ダイカスト生産の連続操業に影響を与える。液状のアルミ・マグネシウム合金は、金型表面への浸食作用が強い。そのため、アルミニウム・マグネシウム合金ダイカスト用金型を製造するためには、金型材料として、焼戻し安定性が高く、600℃程度での冷熱疲労に強く、液体アルミニウム・マグネシウム合金の高温、高圧、高速、高溶損耐性に優れたものが要求される。金型の強度と靭性を高めると同時に、金型材料の潜在能力を引き出し、金型の寿命を向上させるためには、正しい熱処理が必要です。現在、金型製造において一般的に使用されているアルミ・マグネシウム合金ダイカスト用金型鋼は以下の通りです:3Cr2W8V鋼、4Cr5MoSiV1鋼、4Cr3Mo3SiV鋼、4Cr5MoSiV鋼、新鋼種の4Cr5Mo2MnSiV1鋼、3Cr3Mo3VNb鋼などである。
アルミニウム・マグネシウム合金ダイカスト金型の製造ルート
アルミ・マグネシウム合金ダイカスト金型の製造工程は、型抜き→鍛造→球状化焼鈍→機械加工→焼入れ→焼戻し→補修→研削→研磨→窒化(軟窒化)→組立・使用。
アルミニウム・マグネシウム合金ダイカスト金型の強化・靭性化処理プロセス
アルミ・マグネシウム合金ダイカスト金型の強靭化処理とは、金型に要求される構造と性能を得るために、鋼材の組織を変化させることである。熱処理は、金型の材質、金型の形状、大きさ、複雑さなどに基づいて、熱処理工程の仕様を決定する必要があります。
3.1 予熱処理
ダイカスト金型の予熱処理には、連続焼鈍、等温焼鈍、焼入れ焼戻し熱処理の3工程を採用することができる。その目的は、鋼の強度と靭性を向上させる最終熱処理の前に、均一な組織と分散した炭化物を得ることである。連続焼鈍工程は比較的簡単で、より良好な粒状パーライト組織も得られる。複雑な形状で要求の高いダイカスト金型には、等温焼鈍を行うことで、より理想的な粒状パーライト組織を得ることができる。
3.2 焼入れと予熱
ダイカスト金型用鋼は、熱伝導率の悪い高合金鋼が多い。焼入れや加熱の際に予熱措置をとることが多い。予熱の回数や温度は、金型鋼の成分や金型の変形に対する要求によって異なります。焼入れ温度が低く、形状が単純で、変形の要求が低い金型では、焼入れ・加熱時に予熱(800~850℃)を行えば割れは生じない。焼入れ温度が高く、形状が複雑で変形が大きい金型では、二次予熱(600~650℃、800~850℃)が必要です。加熱時に発生する応力を低減すると同時に、金型全体の構造を均一にするためである。
3.3 焼入れ加熱
ダイカスト金型の焼入れ加熱温度は、各鋼種の焼入れ加熱仕様に応じて実施することができる。例えば、3Cr2W8V鋼の焼入れ温度は1050~1150℃であり、H13鋼の焼入れ温度は1020~1100℃である。この2つの鋼の焼入れ温度を上げると、ダイカスト金型の高温強度と耐熱疲労性を高めることができますが、金型の変形が大きくなります。塩浴炉で加熱する場合は、金型表面の酸化脱炭を避けるため、脱酸性の良い塩化バリウム塩浴を使用し、脱酸を頻繁に行う。箱型抵抗炉で加熱する場合は保護雰囲気を採用し、梱包後は一般の箱型抵抗炉で加熱する。ダイカスト金型の焼入れ・加熱保持時間は、炭化物を十分に溶解させ、均一なオーステナイトを得るとともに、良好な高温性能を得るために、適宜延長することが望ましい。一般に塩浴炉の加熱保持係数は0.0分/mmである。
3.4 急冷
油焼入れ速度は速く、良好な性能を得ることができるが、変形や割れの傾向が大きい。一般に、単純な形状で変形要求の小さい油冷ダイカスト金型が使用され、複雑な形状で変形要求の大きいダイカスト金型では、金型の変形や割れを防止するために階層的焼入れを行う必要がある。クエンチ冷却は、クエンチ変形を低減するためにできるだけ遅くする必要があり、真空抵抗炉で加熱し、クエンチし、冷却はガスクエンチを採用することができます。塩浴で加熱急冷し、冷却時にグレード急冷を採用することができます。金型を急冷する場合は、一般に150~200℃に冷却し、浸漬後直ちに焼戻しする。室温まで冷却することはない。
3.5 焼き戻し
ダイカスト金型の硬度は焼戻しによって達成され、ダイカスト金型キャビティの硬度は金型の熱疲労寿命と冷疲労寿命に直接影響する。材質が異なれば、焼入れ温度も異なり、焼戻し温度も異なる。例えば、3Cr2W8V鋼アルミニウムマグネシウム合金ダイカスト金型の硬度は一般的に42~48HRCで、焼戻し温度は一般的に560~620℃を選択しますが、高温焼入れを使用する場合、焼戻し温度は670℃にもなります。1150℃焼入れ、650℃焼戻し後の硬度は45HRC、1050℃焼入れ、650℃焼戻し後の硬度は35HRCである。H13鋼アルミマグネシウム合金ダイカスト金型の硬度は44~50HRCが要求される。H13鋼の二次硬化のピークは500℃の焼戻し時に現れますが、ピークの大きさは焼入れ温度に関係します。焼戻し温度は一般に560~620℃である。焼戻しは2~3回行う。最初の焼戻し温度は低くてもよい。1回目の焼戻し後、硬度を測定する。要求硬度に達していれば、焼戻し温度を20~30℃下げて硬度低下を防ぐ。硬度が高すぎる場合は、硬度の高さに応じて焼戻し温度を適切に調整し、要求硬度を満たすようにする。3回目の焼戻しは靭性を向上させるため、焼戻し温度は2回目の焼戻し温度より高くする。
二次焼戻し温度は30~50℃低い。焼戻しと保持時間は、焼入れ時に発生する応力を除去し、金型クラックの発生を抑えるのに十分な時間とする。1回の焼戻しの保持時間は2hとし、大型金型では保持時間を適宜延長する。ダイカスト金型は、焼入れ後の熱応力や組織応力が大きいため、一般に150~200℃に冷却した直後に焼戻しを行う。
アルミニウム・マグネシウム合金ダイカスト金型の表面強化処理工程
焼入れ・焼戻し後のアルミ・マグネシウム合金ダイカスト金型の表面硬度はあまり高くありません。中子部分は十分な強度と靭性を維持したまま、金型表面の高硬度と耐摩耗性を得るため、また、アルミニウム・マグネシウム合金ダイカスト金型の固着防止性能を向上させるために、金型に表面窒化処理または窒化処理を施すことができます。浸炭処理。
4.1 窒化処理
窒化処理とは、鋼の表面を窒化し、表層の窒素濃度を高める熱処理である。窒化の目的は、金型部品の変形を抑え、アルミニウム・マグネシウム合金ダイカスト金型の表面硬度、耐摩耗性、疲労強度、耐焼付性を向上させ、大気や過熱水蒸気に対する金型の耐食性を向上させ、焼戻しや軟化に対する耐性を向上させることである。ノッチ感度。固体窒化、液体窒化、ガス窒化が一般的な窒化方法です。イオン窒化、真空窒化、電解窒化、高周波窒化などの新技術は、窒化サイクルを大幅に短縮し、高品質の窒化層を得ることができ、企業の経済効率を向上させることができるため、生産に広く使用されている。
4.2 浸炭
ニトロカーバライジングは、アンモニアとアルコール液体(メタノール、エタノール)および尿素、ホルミル糊、トリエタノール糊などの共浸透媒体を加えたものである。一定の温度で熱分解反応を起こし、活性な窒素原子と炭素原子を生成し、アルミニウム・マグネシウム合金でダイカスト化する。金型表面に吸着した後、拡散して金型表層に浸透し、窒素ベースの軟窒化層を得るので、金型はより高い表面硬度、耐疲労性、耐摩耗性、耐食性を得ることができる。軟窒化処理方法には液体法と気体法があり、生産に使用される方法のほとんどは気体軟窒化処理である。H13鋼アルミ合金ダイカスト金型は、高温塩浴炉で550℃×40分と850℃×40分の2段階の予熱処理を行い、1030℃で急冷し、600℃で焼戻し後、580℃でガス軟窒化熱処理を行う。硬度は900HV以上、母材硬度は46~48HRCで、金型の耐摩耗性、耐疲労性、耐食性が大幅に向上し、付着、剥離、傷、腐食がなく、金型の寿命が効果的に向上する。
Conclusion
重要な加工設備であるアルミ・マグネシウム合金ダイカスト金型は、企業の製品品質と経済利益に直接的な影響を与える。調査統計によると、不適切な熱処理工程による金型不良が全体の約50%を占めている。従って、強化・強靭化処理と表面強化処理工程を合理的に選択し、熱処理工程仕様を厳格に管理することは、金型の性能と寿命を向上させる重要な方法である。アルミニウム-マグネシウム合金ダイカスト金型の生産では、金型の使用条件に応じて故障原因を分析・研究し、熱処理工程を合理的に策定して、金型表面の硬度、耐摩耗性、中子の強度と靭性を確保し、金属液の腐食と金型の固着を防止し、不良率を効果的に低減し、金型の寿命を大幅に改善する必要があります。