鍛造とは、鍛造とスタンピングの総称です。鍛造機のハンマー、アンビル、パンチ、あるいは金型を用いてブランクに圧力を加え、塑性変形させることにより、必要な形状や寸法のワークを得る成形加工法である。.
鍛造工程では、ビレット全体が大きな塑性変形を起こし、比較的大きな塑性流動を持つ。スタンピング工程では、ビレットは主に各部分の領域の空間位置を変えることによって形成され、内部には大きな距離の塑性流動はない。鍛造は主に金属部品の加工に使用され、エンジニアリングプラスチック、ゴム、セラミックブランク、レンガブランク、複合材料の成形など、特定の非金属の加工にも使用できます。
冶金産業における鍛造と圧延・伸線は、いずれも塑性加工、すなわち加圧加工であるが、鍛造は主に金属部品の製造に用いられ、圧延・伸線は主に板、条、管などの製造に用いられる。形材、線材などの汎用金属材料。
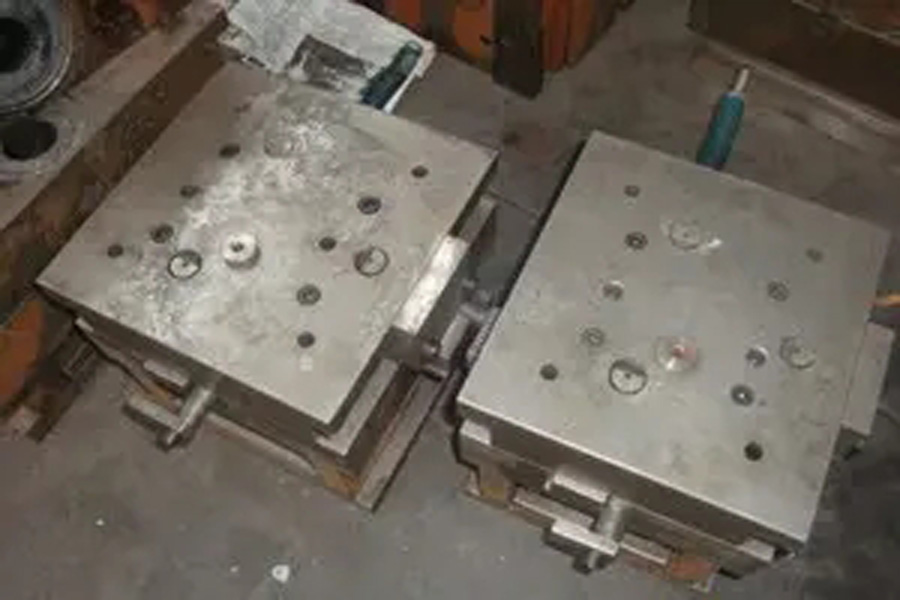
新石器時代の終わり、人類は装飾品や小物を作るために天然の赤銅をハンマーで叩き始めた。中国では紀元前2000年頃から冷間鍛造で道具を作るようになった。例えば、甘粛省武威市の黄日台契家文化遺跡から出土した赤銅の工芸品には、明らかにハンマーで叩いた跡がある。殷代中期には、隕鉄を加熱鍛造して武器を作っていた。春秋時代後期に登場したブロック熔鉱炉は、加熱と鍛造を繰り返して酸化物を押し出したものである。
当初はハンマーに包んで鍛造していたが、後にロープと滑車を引いて重いハンマーを持ち上げ、自由落下させて鍛造する方法が登場した。14世紀以降になると、人力や油圧による落下鍛造が登場する。
1842年、イギリスのナスミスが最初のスチームハンマーを作り、鍛造は動力を応用する時代に入った。その後、鍛造用油圧プレス、モーター駆動のスプリントハンマー、エアー鍛造ハンマー、機械式プレスなどが次々と登場した。スプリントハンマーは、アメリカ南北戦争(1861~1865年)で武器部品の型鍛造に使われたのが最初で、その後ヨーロッパで蒸気式型鍛造ハンマーが登場し、次第に型鍛造技術が普及していった。19世紀末には、近代鍛造機械の基本的なカテゴリーが形成された。
20世紀初頭、自動車の大量生産が始まると、熱間型鍛造は急速に発展し、主要な鍛造工程となった。20世紀半ばには、通常の鍛造用ハンマーに代わって、熱間型鍛造プレス、平型鍛造機、ノンアンビル鍛造ハンマーが次第に普及し、生産性の向上、振動・騒音の低減が図られるようになった。酸化加熱技術の少ない鍛造ブランク、高精度で長寿命の金型、熱間押出、成形圧延、鍛造マニピュレーター、マニピュレーター、自動鍛造生産ラインなどの新しい鍛造プロセスの開発により、鍛造生産の効率と経済効果は向上し続けている。
冷間鍛造の登場は熱間鍛造に先立つ。初期の銅、金、銀片、硬貨はすべて冷間鍛造であった。機械製造における冷間鍛造の応用は、20世紀になって一般化した。冷間圧造、冷間押出し、ラジアル鍛造、スイング鍛造が相次いで開発され、次第に切削なしで精密部品を生産できる効率的な金属鍛造プロセスが形成されるようになった。
初期のスタンピングは、シャベル、鋏、パンチ、ハンドハンマー、アンビルといった簡単な道具を使い、手作業で切断、穴あけ、シャベル、打楽器によって金属板(主に銅板や銅合金板など)を成形していたに過ぎない。銅鑼、シンバル、その他の楽器やポットの製造。中・厚板の生産量の増加、プレス油圧機や機械プレスの発達に伴い、19世紀半ばにはプレス加工も機械化されるようになった。
1905年、米国はコイル状の熱間連続圧延狭幅帯鋼の生産を開始した。1926年には広幅帯鋼の生産を開始した。その後、冷間連続圧延帯鋼が登場した。同時に、厚板と帯鋼の生産量が増加し、品質が向上し、コストが削減された。船舶、鉄道車両、ボイラー、コンテナ、自動車、缶などの生産が発展するにつれて、プレス加工は鋼板の製造工程のひとつとなった。スタンピングは、最も広く使用されている成形プロセスの1つとなっています。
鍛造は主に成形方法と変形温度によって分類される。成形方法によって、鍛造とスタンピングに分けられ、変形温度によって、熱間鍛造、冷間鍛造、温間鍛造、等温鍛造に分けられます。
熱間鍛造は金属の再結晶温度以上で行われる。温度を上げると金属の塑性が向上し、ワークの内部品質が向上し、割れにくくなる。また、高温は金属の変形抵抗を低下させ、必要な鍛造機械のトン数を減らすことができる。しかし、熱間鍛造工程が多く、ワークの精度が悪く、表面が滑らかでなく、鍛造品が酸化、脱炭、焼けを起こしやすい。
冷間鍛造とは、金属の再結晶温度より低い温度で行う鍛造のことである。一般に冷間鍛造とは、特に常温での鍛造を指し、常温より高く再結晶温度を超えない温度での鍛造を温度という。鍛造である。温間鍛造は精度が高く、表面が滑らかで変形しにくい。
常温の冷間鍛造で成形された部品は、形状や寸法精度が高く、表面が滑らかで、加工工程が少なく、自動化が容易である。冷間鍛造や冷間スタンピングの部品の多くは、切削加工なしでそのまま部品や製品として使用できる。しかし、冷間鍛造では金属の塑性が低いため、変形時に割れが発生しやすく、変形抵抗が大きいため、大きなトン数の鍛造機械が必要となる。
等温鍛造とは、成形プロセスを通じてブランクの温度が一定であることを意味する。等温鍛造は、ある種の金属が一定の温度で高い塑性を持つことを最大限に利用するため、あるいは特定の構造や特性を得るために行われる。等温鍛造は、金型とブランクの温度を一定に保つ必要があるため、コストが高く、超塑性成形のような特殊な鍛造加工にしか用いられない。
鍛造は金属組織を変化させ、金属特性を向上させることができる。インゴットを熱間鍛造した後、元の鋳造時のゆるみ、気孔、マイクロクラックなどを圧縮または溶接し、元の樹枝状結晶を破壊して結晶粒を微細にし、同時に元の炭化物の偏析や凹凸を分布変化させて組織を均一にし、内部がコンパクトで、均一で、きめが細かく、総合性能がよく、安全に使用できる鍛造品を得ることができる。熱間鍛造によって鍛造品が変形した後、金属は繊維状組織となり、鍛造品が変形した後、金属の結晶は整然となる。
鍛造とは、金属を塑性流動させて目的の形状のワークを作ることである。外力によって塑性流動が発生した後も金属の体積は変化せず、金属は常に最も抵抗の少ない部分に流れる。生産現場では、アプセットや絞り、リーマ、曲げ、絞りなどの変形を実現するために、このルールに従ってワークの形状を制御することが多い。
鍛造品の寸法は正確で、大量生産の組織化に寄与する。金型鍛造、押し出し、スタンピングなどの用途の寸法は正確で安定しています。高効率鍛造機械と自動鍛造生産ラインは、特殊な大量生産または大量生産を組織するために使用することができます。
鍛造の生産工程には、成形前のブランクの型抜き、ブランクの加熱と前処理、成形後のワークの熱処理、洗浄、校正、検査が含まれる。一般的に使用される鍛造機械には、鍛造ハンマー、油圧プレス、機械プレスなどがある。鍛造ハンマーは衝撃速度が大きく、金属の塑性流動を助長するが、振動が発生する。油圧プレスは静的鍛造を使用し、金属を通して鍛造し、構造を改善するのに適しており、作業は安定しているが、生産性は低い。機械プレスはストロークが固定されており、機械化および自動化を実現するのが容易である。
将来、鍛造工程は鍛造部品の内部品質を向上させ、精密鍛造と精密スタンピング技術を開発し、より高い生産性と自動化を備えた鍛造設備と鍛造生産ラインを開発し、フレキシブルな鍛造成形システムを開発し、新しい鍛造材料と鍛造加工方法を開発するなどの発展を遂げる。
鍛造品の内部品質を向上させることは、主にその機械的特性(強度、塑性、靭性、疲労強度)と信頼性を改善することである。そのためには、金属塑性変形理論のより良い適用、より優れた固有の品質を持つ材料の適用、正しい鍛造前加熱と鍛造熱処理、鍛造部品のより厳格でより広範な非破壊検査が必要である。
切削加工を減らし、切削加工をしないことは、機械産業が材料利用を改善し、労働生産性を向上させ、エネルギー消費を削減するための最も重要な対策であり、方向性である。より少ない鍛造ブランク、酸化加熱なし、高硬度、耐摩耗性、長寿命の金型材料と表面処理方法の開発は、精密鍛造と精密スタンピングの適用拡大に寄与する。