自動車パワーシステム用部品の製造に粉末冶金(P / M)プロセスの使用が増え続けている。粉末冶金プロセスで製造された部品には、多くの重要かつユニークな利点がある。これらの部品に意図的に残された残留多孔質構造は、自己潤滑と遮音に適しています。従来の鋳造プロセスでは製造が困難または不可能な複雑な合金も、P / M技術を使用すれば製造できます。この技術で製造された部品は通常、加工能力がほとんどないため、安価で材料の無駄が少ない。残念ながら、これらの特徴の魅力の裏側で、P / M部品は機械加工が困難です。
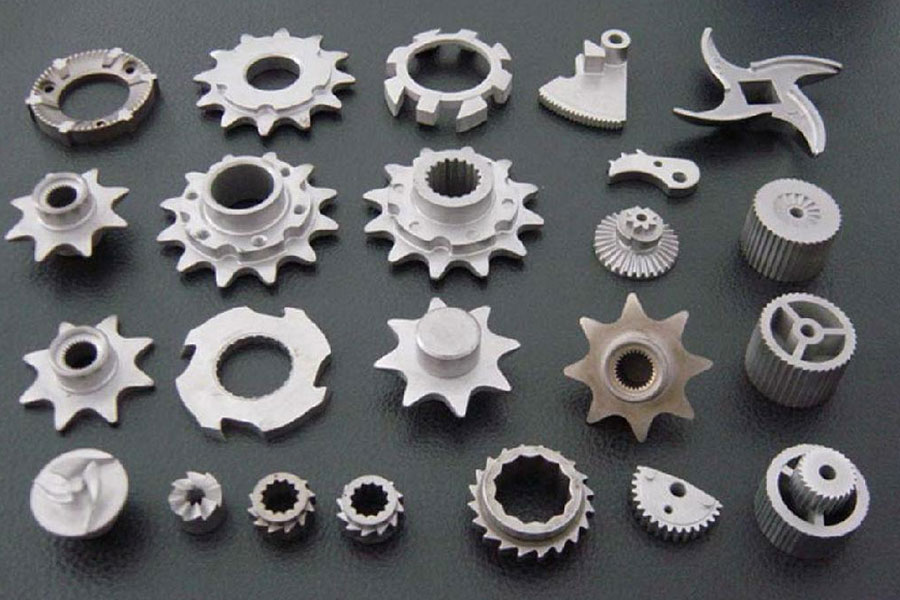
P/M業界の当初の目的の1つは、すべての加工をなくすことであったが、この目標はまだ達成されていない。ほとんどの部品は「最終形状に近い状態」にしかできず、まだ仕上げが必要である。
しかし、鋳造品や鍛造品に比べ、P / M部品から除去する必要がある材料は少量で、典型的な耐摩耗性材料である。
多孔質構造はP / M部品に幅広い用途を持たせる特徴の一つですが、多孔質構造によって工具寿命も損なわれます。多孔質構造は油や音を蓄えることができるが、微細な断続切削にもつながる。穴から固体粒子を往復する際、工具先端は連続的に衝撃を受け、非常に小さな疲労破壊変形や切れ刃に沿った微細な刃先の崩壊を引き起こす可能性がある。さらに悪いことに、粒子は通常非常に硬い。測定された材料のマクロ硬度が20~35度であっても、部品の粒径は60度にも達する。このような硬い粒子は、激しく急速なエッジ摩耗を引き起こす。多くのP / M部品は熱処理が可能であり、熱処理後の材料の硬度と強度は高くなる。最後に、焼結および熱処理技術と使用されるガスにより、材料の表面には硬質で耐摩耗性の酸化物および/または炭化物が含まれます。
P/M部品の性能
機械加工性を含むP/M部品の特性のほとんどは、合金の化学組成だけでなく、多孔質構造の気孔率レベルにも関係している。多くの構造部品の気孔率は15%~20%に達する。濾過装置として使用される部品の気孔率は50%に達することもある。一方、鍛造部品や股関節部品の気孔率はわずか1%以下である。これらの材料は、より高いレベルの強度を達成できるため、自動車や航空機の用途で特に重要になってきている。P / M合金の引張強さ、靭性、および延性は、密度の増加とともに増加し、気孔率は工具先端に有害であるため、被削性も改善される可能性がある。気孔率の増加は部品の遮音性能を向上させる。標準的な部品の減衰振動は、P / M部品では大幅に減少し、これは工作機械、空調用ブローパイプ、空気圧工具にとって非常に重要である。高い気孔率は、自己潤滑歯車にも必要です。
機械加工の難しさ
P / M産業の継続的な発展の目標の1つは機械加工をなくすことであり、P / Mプロセスの主な魅力の1つは、少量の加工で済むことであるが、多くの部品は、より高い精度やより良い表面仕上げを得るために後処理を必要とする。残念ながら、これらの部品の加工は非常に難しい。発生する問題のほとんどは、気孔率に起因するものである。気孔は切れ刃の微小疲労につながる。切れ刃は常に切り込んだり抜いたりしている。それは粒子と穴の間を通過する。小さな衝撃が繰り返されると、刃先に小さな亀裂が生じる。
これらの疲労亀裂は、刃先が崩壊するまで成長する。この種の微小チッピングエッジは通常非常に小さく、通常は通常の研磨摩耗を示す。多孔質はまた、P / M部品の熱伝導率を低下させるため、刃先の温度が高くなり、クレーター摩耗や変形の原因となる。内部でつながった多孔質構造は、切削領域から切削液が排出される経路となる。これは、特にドリル加工において、高温クラックや変形の原因となる。
内部多孔質構造による表面積の増大は、熱処理中の酸化や炭化にもつながる。前述したように、これらの酸化物や炭化物は硬く、耐摩耗性に優れている。
多孔質構造はまた、部品の硬度測定に失敗をもたらし、これは非常に重要である。P / M部品のマクロ硬度を意図的に測定する場合、それは穴硬度の要素を含んでいます。多孔質構造は構造の崩壊につながり、比較的柔らかい部品という誤った印象を与えます。粒子はもっと硬い。上記のように、その差は劇的である。
PM部品に介在物が存在することも不利である。加工中、これらの粒子は表面から引き上げられ、工具の前で擦られると部品表面に傷やスクラッチが形成される。これらの介在物は通常大きく、部品の表面に目に見える穴が残ります。
炭素含有量の違いは、被削性の不一致につながる。例えば、fc0208合金の炭素含有量は0.6%から0.9%である。炭素含有量が0.9%のバッチは比較的硬く、工具寿命が悪い。一方、炭素含有量が0.どちらの合金も許容範囲内である。
最終的な加工の問題は、P/M部品で発生する切削のタイプに関連している。部品は最終形状に近いため、切削深さは通常非常に浅くなります。そのため、自由な切れ刃が必要となる。切れ刃に切り屑が堆積すると、しばしば微小チッピングが発生する。
加工技術
これらの問題を克服するために、いくつかの技術(業界独自のもの)が適用されている。表面の多孔質構造は、浸透によって密閉されることが多い。通常、追加のフリーカットが必要となる。最近では、粉末の清浄度を高め、熱処理中の酸化物や炭化物を減少させるように設計された、改良された粉末製造技術が使用されている。
閉じた表面の多孔質構造は、金属(通常は銅)またはポリマーの浸透によって達成される。浸潤は潤滑剤として作用すると推測されている。ほとんどの実験データは、本当の利点は表面の多孔質構造を閉じることにあり、それによって切れ刃の微小疲労を防ぐことにあることを示している。びびりの低減は、工具寿命と仕上げ面精度を向上させる。浸潤の最も劇的な利用法は、多孔質構造が閉鎖されると工具寿命が200%向上することを示している。
MNS、s、MoS2、MgSiO3、BNなどの添加剤は、工具寿命を延ばすことが知られている。これらの添加剤は、切り屑を被削材から分離しやすくし、切り屑を破砕し、切り屑の堆積を防ぎ、切れ刃を潤滑することで、被削性を向上させる。添加剤の量を増やすと被削性は向上するが、強度と靭性は低下する。
焼結・熱処理炉ガスを制御する粉末微粒化技術により、介在物や表面酸化炭化物の発生を最小限に抑えたクリーンな粉末・部品の製造が可能。
工具材料
P / M産業で最も広く使用されている工具は、良好な表面仕上げの条件下で、耐摩耗性、耐エッジクラック性、およびチップフリーである材料です。これらの特性は、あらゆる加工作業、特にP / M部品に有用である。このカテゴリーに含まれる工具材料は、立方晶窒化ホウ素(CBN)工具、非コーティングおよびコーティングされたサーメット、改良コーティングされた焼結超硬合金である。
CBN工具は、その高い硬度と耐摩耗性が魅力である。この工具は、ロックウェル硬度45以上の鋼や鋳鉄の加工に長年使用されてきた。しかし、P / M合金のユニークな特性と、微小硬度とマクロ硬度の大きな違いにより、CBN工具はロックウェル硬度25のP / M部品にも使用できる。重要なパラメータは粒子の硬度である。粒子の硬度がロックウェル50度を超える場合、CBN工具はマクロ硬度の値に関係なく使用できる。これらの工具の明らかな限界は、靭性の欠如である。断続切削や気孔率が高い場合には、ネガティブ面取りや重ホーニングを含む刃先補強が必要である。単純な軽切削であれば、ホーニングされた切れ刃でも可能である。
CBNには有効な材料がいくつかある。最も靭性に優れた材料は、主にCBN全体から構成されている。靭性に優れているため、荒加工にも使用できる。その限界は通常、表面仕上げに関係する。それは、工具を構成する個々のCBN粒子によって大きく左右される。粒子が切れ刃から脱落すると、被削材の表面に影響を及ぼす。しかし、微粒子工具が1つの粒子を脱落させるほど深刻ではない。
通常使用されるCBN材料は、CBN含有量が高く、粒径は中程度である。CBN仕上げ用ブレードは細粒で、CBN含有量は低い。軽い切削と表面仕上げが必要な場合、または加工される合金が特に硬い場合に最も効果的です。
多くの切削用途において、工具寿命は材料の種類に依存しない。言い換えれば、どのCBN材料でも同様の工具寿命を達成できる。このような場合、材料の選択は主に各切刃の最低コストに基づいて行われる。1つの丸刃はCBN上面全体を持ち、4つ以上の切れ刃を提供できるため、4つのはめ込み式CBN刃よりも安価である。
P / M部品の硬度がロックウェル35度より低く、粒子の硬度がその範囲内にある場合、通常サーメットが選択肢のひとつとなる。サーメットは非常に硬く、切り屑の堆積を効果的に防ぐことができ、高速回転にも耐えることができる。さらに、サーメットは常に鋼やステンレスの高速加工や仕上げ加工に使用されてきたため、通常、成形部品に近い理想的な幾何学的溝を持っている。
Todayのサーメットは冶金学的に複雑で、最大11の合金元素がある。通常、TiCN粒子とNi Mo接着剤から焼結される。TiCNは、サーメットをうまく使用するために重要な硬度、耐切り屑性、化学的安定性を提供する。さらに、これらの工具は通常、接着剤の含有量が高いため、良好な靭性を持つ。一言で言えば、P / M合金を効果的に加工するためのすべての特性を備えている。炭化タングステン焼結超硬合金のように、結合剤の含有量が多いほど靭性が向上するサーメットもあります。
比較的新しい開発として知られているのは、中温化学気相成長法(mtcvd)もP / M産業に利点をもたらすということである。Mtcvdは、従来の化学気相成長法(CVD)の耐摩耗性と耐クレーター摩耗性をすべて維持しながら、靭性も客観的に向上させる。靭性の向上は、主にクラックの減少によるものです。コーティングは高温で蒸着され、炉内で冷却される。熱膨張が一定しないため、工具が室温に達するとコーティングにクラックが入る。平らなガラスの傷と同様に、このクラックは刃先の強度を低下させる。mtcvdの成膜温度が低いほど、クラックの発生頻度が低くなり、切れ刃の靭性が向上する。
CVD コーティングと mtcvd コーティングの基材が同じ特性で、エッジドレッシングを施した場合、両者の靭性の違いを示すことができる。エッジ靭性が要求される用途では、CVD コーティングよりも mtcvd コーティングの方が優れている。分析によると、多孔質構造を持つP / M部品を加工する場合、エッジ靭性が重要である。MtcvdコーティングはCVDコーティングよりも優れている。
物理蒸着(PVD)コーティングは、mtcvdやCVDコーティングよりも薄く、耐摩耗性に劣る。しかし、PVDコーティングはアプリケーションでの大きな衝撃に耐えることができます。PVDコーティングは、切削加工が摩耗性で、CBNやサーメットでは脆すぎ、優れた表面仕上げが必要な場合に有効です。
例えば、C-2超硬合金の切れ刃は、180 m/分の線速と0.15 mm/回転の送り速度でfc0205を加工できる。20個の部品を加工すると、切り屑の堆積が微小な崩壊を引き起こす可能性がある。PVD窒化チタン(TIN)コーティングを使用すると、切り屑の堆積が抑制され、工具寿命が延びる。今回の試験で錫コーティングを使用した場合、P / M部品の研磨摩耗特性は、TiCNコーティングの方が効果が期待できる。TiCNは錫とほぼ同等の耐切り屑堆積性を持つが、錫よりも硬く耐摩耗性に優れている。
多孔質構造は重要であり、fc0208合金の被削性に影響する。ポーラス構造や特性が変われば、工具材料もそれに応じた利点がある。密度が低い場合(6.4g/cm3)、マクロ硬度は低い。この場合、mtcvdコーティング超硬合金が最も優れた工具寿命を提供する。刃先の微小疲労は非常に重要であり、刃先の靭性も非常に重要である。この場合、靭性の良いサーメット刃が最大の工具寿命を提供する。
同じ合金を密度6.8g/cm3で製造する場合、刃先のクラックよりも摩耗の方が重要になる。この場合、mtcvdコーティングが最高の工具寿命を提供する。PVDコーティングされた超硬合金は、2種類の極めて硬い部品の試験に使用され、刃先に触れると割れる。
速度が速くなると(直線速度が毎分300メートル以上)、サーメットはもちろん、被覆サーメットでもクレーター摩耗が発生する。特にコーティング超硬合金の刃先靭性が良い場合は、コーティング超硬合金の方が適している。Mtcvdコーティングは、コバルトを多く含む超硬合金に特に効果的である。
サーメットは、旋削加工とボーリング加工で最も一般的に使用される。PVDコーティングされた超硬合金は、より低速で、よりビルドアップに注意する必要があるため、ねじ加工に最適です。