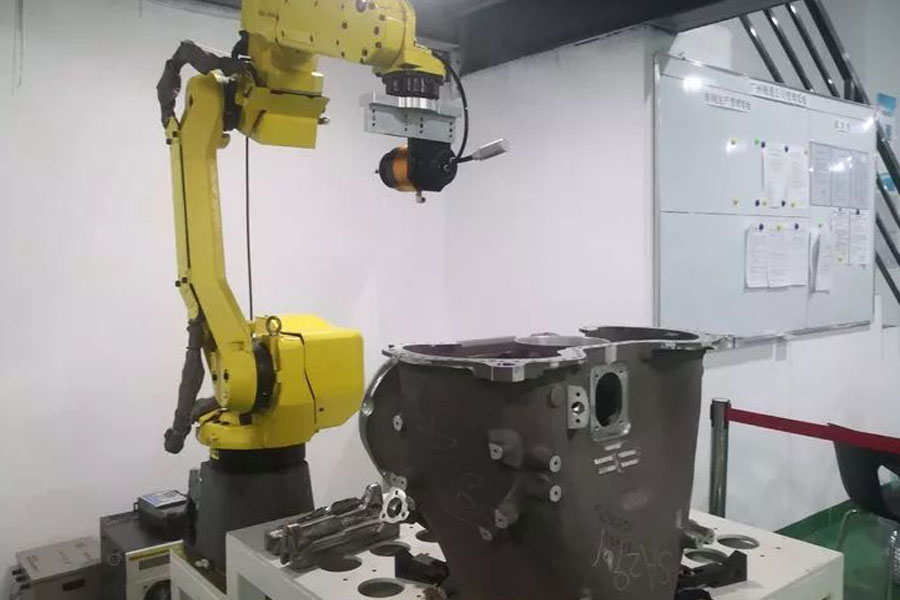
ダイカスト部品のバリ取りを行う企業は、多くの人手と資材を投入する必要がある。バリ取り作業者はダイカスト作業者の1~2倍となり、人件費がかさむ。バリ製造現場は埃っぽく、うるさい。現代の若者はこの種の作業に従事したがらず、企業にとって作業員の確保が難しい。自動バリ取りは人件費を大幅に削減することができ、これは将来の発展方向でもある。しかし、自動バリ取りは、鋳物の一貫性に対してより高い要求を突きつける。バリを除去しない場合のダイカスト鋳物のバリの種類、厚さ、長さ、バリを除去した後の鋳物の外観。金型のパーティング面の隙間については、鋳物の冷却時の収縮変形による寸法変動がマシニングセンターとロボットの認識範囲を超えると、ダウンタイムが発生し、鋳物が損傷し、工具が損傷し、バリ取りの効果が設計要件を満たさなくなる。
アルミ合金ダイカストのバリ
ダイカスト部品のバリの原因は、ダイカストマシン、ダイカスト金型、ダイカスト工程のダイカストの3大要素に通じる。ダイカスト工程では、金型温度やアルミ溶湯温度が高すぎたり、鋳造圧力が高すぎたりするとバリが発生しやすく、ダイカストマシンでは、型締力が不足すると金型にもバリが発生し、ダイカスト金型では、金型パーティング面や中子抜きピン、エジェクターピンの穴など、製造精度が不十分だとバリが発生しやすくなります。ホイールハブのパーティング面には大きなバリが付き、バリ取りの作業負担が増える。金型のバルジング力によっても、鋳物のサイズが公差から外れて厚くなり、原料のアルミの使用量が増える。この場合、生産を停止して対策する必要がある。入れ子端面、面取り面、内孔にバリがある。入れ子の端面は加工されていないので、バリを清掃する必要がある。突合せ穴がアルミと皮の連結で完全に閉じられているため、バリ清掃の難易度が高い。
バリの標準サイズ
バリの厚みを確認するため、ダイカスト金型にテーパー状のモールドギャップを設けた。アルミ素材はADC12、温度は660℃、鋳造圧力は740Kgf/cm2。鋳造検証の結果、肉厚が0.09mm以上では成形が明確であり、肉厚が0.09mm未満で形状が0.06mm以上では成形が連続しないことがわかった。
バリの長さを確認するために、ダイカスト金型に図3の金型分割面を隙間を変えて作成し、バリの長さをテストします。肉厚が0.08mmの場合、鋳造体からのはみ出し長さは約4mm、肉厚が0.07mmの場合、鋳造体からのはみ出し長さは約2mm、肉厚が0.06mm以下の場合、鋳造体からのはみ出し 長さは1mm以下であり、形成しにくく、アルミ皮膜が粉のようになり、ダイカストのショットブラストで完全に除去できる。上記のテストによると、鋳バリの必要条件は:ダイカスト金型製造時の隙間C≧0.07mmです。
バリ・タイプ
ダイカスト鋳物のバリは、パーティングラインバリと鋳造工程で発生するバリ、金型の異常クラックで発生するバリの3つに分けられる。バットタッチホール、アルミクランプ、ネスティング、エジェクタートレースバリはすべてパーティングラインバリ、凸ハルは亀裂バリ、オーバーフロー、ゲートは鋳造工程バリです。上記3種類のバリの厚みと形状はそれぞれ要求が異なります。添付の表はバリの長さと厚さの基準です。この基準はダイカスト工程です。金型保存工程はバリ工程が適格かどうかを判断する基準になります。各メーカーの癖やバリ取り方法によって補正が可能です。.この標準はまた、ロボットのバリ取りを鋳物のバリ状態を制御するための基礎となります。
ダイカストバリ取りの基本原理
バリ取りツール
手動バリ取りの主な工具には、スローター、パンチ、ヤスリなどがあり、空気圧式動力工具には、ベルトマシン、グラインダー、グラインダーなどがあり、ダイカストバリ取り装置には、グラインダー、マシニングセンター、ロボットなどがある。1つは空気式リーマで、閉じた穴(<2mm)を直接貫通させ、穴のバリ、オーバーフローとゲートのバリを除去することができます。バリの標準は一流の標準に達することができる:なし;二流の標準は0.2mm以下;第二の工具は研磨機で、パーティングラインのバリ、エジェクターマーク、凸状外皮、亀裂、タイピング表面のバリを除去することができ、さらに研磨効果;第三のタイプはベルト機で、パーティング表面のバリ、マンドレルマーク、亀裂のバリを除去することができる。これら3つのツールを使用するロボットバリ取りは、基本的に鋳物のバリの90%以上を除去することができます。
手動バリ取りの主な工具には、スローター、パンチ、ヤスリなどがあり、空気圧式動力工具には、ベルトマシン、グラインダー、グラインダーなどがあり、ダイカストバリ取り装置には、グラインダー、マシニングセンター、ロボットなどがある。1つは空気式リーマで、閉じた穴(<2mm)を直接貫通させ、穴のバリ、オーバーフローとゲートのバリを除去することができます。バリの標準は一流の標準に達することができる:なし;二流の標準は0.2mm以下;第二の工具は研磨機で、パーティングラインのバリ、エジェクターマーク、凸状外皮、亀裂、タイピング表面のバリを除去することができ、さらに研磨効果;第三のタイプはベルト機で、パーティング表面のバリ、マンドレルマーク、亀裂のバリを除去することができる。これら3つのツールを使用するロボットバリ取りは、基本的に鋳物のバリの90%以上を除去することができます。
マシニングセンターのバリ取り
ロボットの負荷問題や動作速度の低さを考慮すると、手作業に代わる効率は理想的な状態に達しておらず、マシニングセンタのバリ取りが必要になっている:トルクが大きく、工具交換速度が速く、効率が高い。既存のダイカストメーカーでは、5軸以上のマシニングセンタを採用して自動バリ取りを行っているところが増えており、期待通りの成果を上げている。使用効果の評価から、自動バリ取り機は2人の作業員の代わりになる。
自動バリ取りの一般要件
自動的にバリを除去するために、第一に鋳物の寸法公差を明確にしてブランクの安定性を確保し、第二に鋳型のバッチ管理を行い、同時にバリの変化の原因となる鋳造プロセスを管理する。それぞれの重要な工程は、まず鋳物のバリ状態の安定性を確保します。
ダイカスト部品の外観等級基準
ダイカストバリの外観基準は3段階に分類される。
記事で言及されている鋳物の寸法精度、変形、バリの外観基準は、すべてクラスⅡの外観を指している。
ダイカスト用バリ規格の工学的応用
具体的なダイカスト部品については、各種規格を参照し、ダイカスト工程バリの外観基準を策定する。実際の生産においてのみ、各レベルの人員は統一的な理解を持ち、外観の一貫した標準に達することができる。同時に、需要側の特別な要求を考慮し、標準に反映する必要がある。
結論として
手動バリ取りであれ、自動バリ取りであれ、企業はダイカスト部品のバリを制御可能な状態にしなければならない。バリが基準範囲を超えた場合、ダイカスト工程、金型隙間、寸法公差基準などを調査する必要がある。自動装置では使用条件を満たせないと判断され、自動バリ取り技術は否定される。自動バリ取りの精度は手動バリ取りより高く、バリ取り後の外観の安定性も良い。