材料の加工性に影響を与える主な要因は何ですか?
鋼の化学組成は非常に重要である。鋼の合金組成が高いほど、加工は難しくなる。炭素含有量が増えると、金属の切削性能は低下する。
鋼の構造も金属切削性能にとって非常に重要である。さまざまな構造には、鍛造、鋳造、押出、圧延、機械加工がある。鍛造品と鋳造品は、機械加工が非常に難しい表面を持っています。
硬度は金属の切削性能に影響する重要な要素である。一般的に、鋼が硬いほど加工は難しくなる。高速度鋼(HSS)は、硬度330~400HBまでの被削材を加工できます。高速度鋼+TiNコーティングは、硬度45HRCまでの被削材を加工できます。硬度65~70HRCの被削材には、超硬合金、セラミック、サーメット、立方晶窒化ホウ素(CBN)を使用する必要があります。
非金属介在物は一般的に工具寿命に悪影響を及ぼす。例えば、純粋なセラミックであるAl2O3(アルミナ)は非常に研磨性が高い。
最後のものは残留応力で、金属切削性能の問題を引き起こす可能性がある。多くの場合、粗加工の後に応力除去加工を行うことが推奨される。
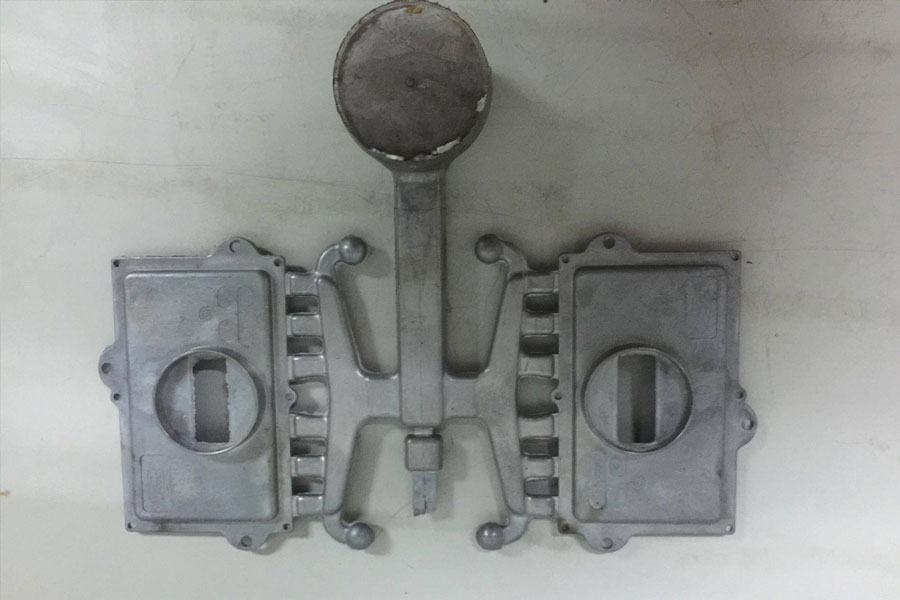
鋳鉄の切削特性は?
一般的に言えば、そうだ:
鋳鉄の硬度と強度が高ければ高いほど、金属切断性能は低下し、ブレードやカッターに期待される寿命も短くなる。金属切削生産に使用されるほとんどの種類の鋳鉄は、一般に良好な金属切削性能を持つ。金属切削性能は構造に関連しており、より硬いパーライト鋳鉄は加工も難しい。片状黒鉛鋳鉄と可鍛鋳鉄は優れた切削特性を持つが、ダクタイル鋳鉄はかなり悪い。
鋳鉄を加工する際に発生する主な摩耗の種類は、摩耗、付着、拡散摩耗です。摩耗は主に炭化物、砂粒子、硬い鋳物の皮によって引き起こされます。付着摩耗は、低い切削温度と切削速度で発生します。鋳鉄のフェライト部分は刃に最も溶着しやすいが、これは切削速度と温度を上げることで克服できる。
一方、拡散摩耗は温度に依存し、特に高強度鋳鉄鋼種を使用した場合、高い切削速度で発生する。これらの鋼種は変形に対する耐性が高いため、高温になる。この摩耗は鋳鉄と切削工具の相互作用に関係するため、鋳鉄の中には、良好な工具寿命と表面品質を得るために、セラミックまたは立方晶窒化ホウ素(CBN)切削工具を使用して高速で加工する必要があるものもある。
一般的に、鋳鉄の加工に要求される代表的な工具特性は、高い熱硬度と化学的安定性であるが、プロセス、被加工物、切削条件にも関係する。刃先には、靭性、耐熱疲労性、刃先強度が要求される。鋳鉄の切削の満足度は、刃先の摩耗がどのように進行するかによって決まります。急激な鈍化とは、高温の亀裂や刻み目によって刃先が早期に破損すること、ワークの損傷、表面品質の低下、過度のうねりなどを意味します。通常の逃げ面摩耗、バランス、シャープな切れ刃は、一般的に努力が必要なものである。
金型製造における主な、そして一般的な加工手順とは?
切断工程は少なくとも3つの工程に分けられるべきである:
荒加工、中仕上げ加工、仕上げ加工、時には超仕上げ加工(主に高速切削用途)。残削加工はもちろん、中仕上げ加工の後に仕上げ加工に備える。各工程では、次の工程のために均一なマージンを残す努力が必要であり、これは非常に重要である。工具経路の方向や作業量が急激に変化することがほとんどなければ、工具の寿命が延び、より予測しやすくなる可能性がある。可能であれば、仕上げ工程は専用の工作機械で行うべきである。そうすることで、デバッグや組み立ての時間が短縮され、金型の幾何学的精度と品質が向上する。
これらの異なるプロセスで、どのようなツールを使うべきか?
粗加工工程:丸刃フライスカッター、ボールエンドミルカッター、ノーズ円弧半径の大きいエンドミルカッター。
半仕上げ工程:丸刃フライス(直径10~25mmの丸刃フライス)、ボールエンドフライス。
仕上げ加工:丸刃フライスカッター、ボールエンドミルカッター。
残留フライス加工:丸刃フライスカッター、ボールエンドミルカッター、縦型フライスカッター。
特殊工具のサイズ、形状、材種の組み合わせ、切削パラメータ、適切なフライス加工方法を選択し、切削工程を最適化することが非常に重要です。
使用可能な高生産性ツールについては、金型製作用カタログC-1102:1を参照。
カッティングのプロセスで最も重要な要素はありますか?
切削加工における最も重要な目標のひとつは、各工程における各工具の加工代を均一にすることである。つまり、特に荒加工や中仕上げ加工では、径の異なる(大から小まで)工具を使用しなければならない。いつでも主な基準は、各工程で金型の最終形状にできるだけ近づけることである。
各工具に均一な加工代を与えることで、常に高い生産性と安全な切削工程を実現します。ap/ae(軸方向切り込み量/半径方向切り込み量)が変化しない場合、切削速度と送り速度も常に高いレベルに維持することができます。このようにすると、刃先への機械的作用や加工負荷の変化が少ないので、発生する熱や疲労も少なくなり、工具寿命が延びる。後工程が一部の中仕上げ工程、特に全仕上げ工程であれば、無人加工や部分的な無人加工を行うことができる。また、高速切削加工用途では、材料加工代を一定にすることが基本的な基準となる。
加工代が一定であることのもう一つの利点は、工作機械のガイドレール、ボールねじ、主軸ベアリングへの悪影響が小さいことである。
金型荒加工用工具として丸刃フライスが最も一般的なのはなぜですか?
キャビティの粗加工にスクエアショルダーのフライスカッターを使用すると、中仕上げ加工で段差のある切削代が大きく削られる。これでは切削力が変化し、工具が曲がってしまう。その結果、仕上げ加工に不均一な削り代が残り、金型の幾何学的精度に影響を与えることになります。ノーズが弱いスクエアショルダーのフライスカッター(三角形のインサート付き)を使用すると、予測できない切削効果が得られます。また、三角形やダイヤモンドのインサートは、半径方向の切削力が大きくなり、インサートの切れ刃の数が少ないため、経済的な荒加工用工具ではない。
一方、円形インサートは、様々な材料で、あらゆる方向に加工することができる。使用すれば、隣接するツールパス間の移行がよりスムーズになり、半仕上げのための加工をより小さく均一に残すこともできる。余白。丸刃の特徴のひとつは、生成される切りくずの厚さが可変であることです。これにより、他の多くのチップよりも高い送り速度を使用することができます。
丸チップの進入角度は、ほぼゼロ(非常に浅い切削)から90度まで変化し、切削動作は非常にスムーズです。最大切削深さでは、進入角度は45度である。外周を持つ直線壁に沿って切削する場合、進入角度は90度である。丸刃工具の強度が大きい理由もここにある。荒加工や半荒加工では、CoroMill200(金型製造用カタログC-1102:1参照)のような丸刃のフライスカッターを第一選択として必ず使用する。5軸切削では、特に制約がないため、丸刃チップが非常に適しています。
優れたプログラミングを使用することで、ラウンドインサートミリングカッタは、ボールエンドミルに取って代わることができます。振れの小さい丸刃は、細かく研磨されたポジティブすくい角と軽い切削形状と組み合わされ、中仕上げ加工や一部の仕上げ加工にも使用できます。
有効切削速度(ve)とは何か、そしてなぜそれが常に高い生産性の有効直径上の有効切削速度の基本的な計算のために非常に重要なのか。
テーブル送りは、ある切削速度における回転速度に依存するため、実効速度を計算しなければ、テーブル送りを誤って計算することになる。
切削速度の計算に工具の呼び径(Dc)を使用すると、切削深さが浅い場合、実効または実際の切削速度は計算速度よりかなり低くなります。例えば、丸インサートCoroMill200工具(特に小径範囲)、ボールエンドミル、ラージノーズ円弧半径エンドミル、CoroMill390エンドミルなど(これらの工具については、Sandvik Coromant社の金型製造サンプルC-1102:1を参照してください)。その結果、計算上の送り速度も大幅に低下し、生産性が著しく低下する。さらに重要なことは、工具の切削条件がその能力と推奨される適用範囲よりも低くなることである。