About 80% of the failures of mechanical parts are caused or induced by various forms of wear. Abrasion failure not only causes a lot of waste of resources, but also may directly cause huge economic losses. Mechanical parts not only require high wear resistance, but also must have high impact toughness, so as to meet the needs of modern mechanical engineering. Therefore, it is an important way to reduce the failure of mechanical parts to develop a new generation of wear-resistant steel with martensitic structure combined with modern rolling technology and prepare high-strength and high-toughness low-carbon microalloy wear-resistant materials.
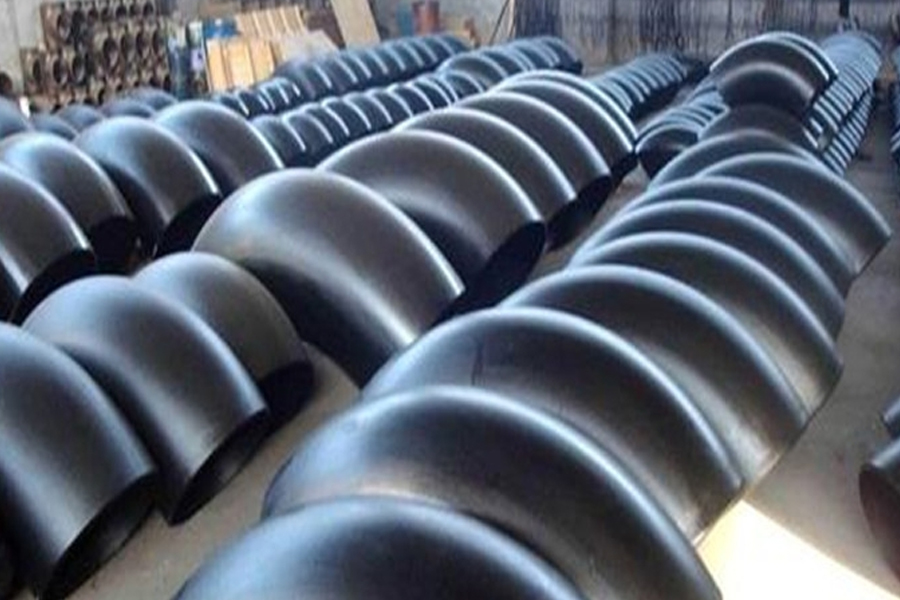
According to the performance requirements of the wear-resistant steel, a reasonable chemical composition of the wear-resistant steel is designed, and the elements such as medium C, low Mn, Si, Nb, Ni, Cr, Mo, V, B are used for alloying, so that the steel has a relatively high quality after quenching. High hardness and sufficient plasticity and toughness ensure that the material has good hardenability, hardenability and wear resistance. The specific functions of each element in wear-resistant steel are as follows:
By optimizing the chemical composition design of the wear-resistant steel and fully considering the interaction between the alloying elements, two martensitic wear-resistant steel materials with two strength levels are obtained. Preliminary research results show that these two refined martensitic lath microstructures can be obtained in the two-stage rolling process of controlled rolling and controlled cooling, which simplifies the process, and there is no obvious difference between the two microstructures.