Shackles can be seen all the time in life, so do we know about shackles? Let Minghe introduce the improvement of forging process of shackle forging
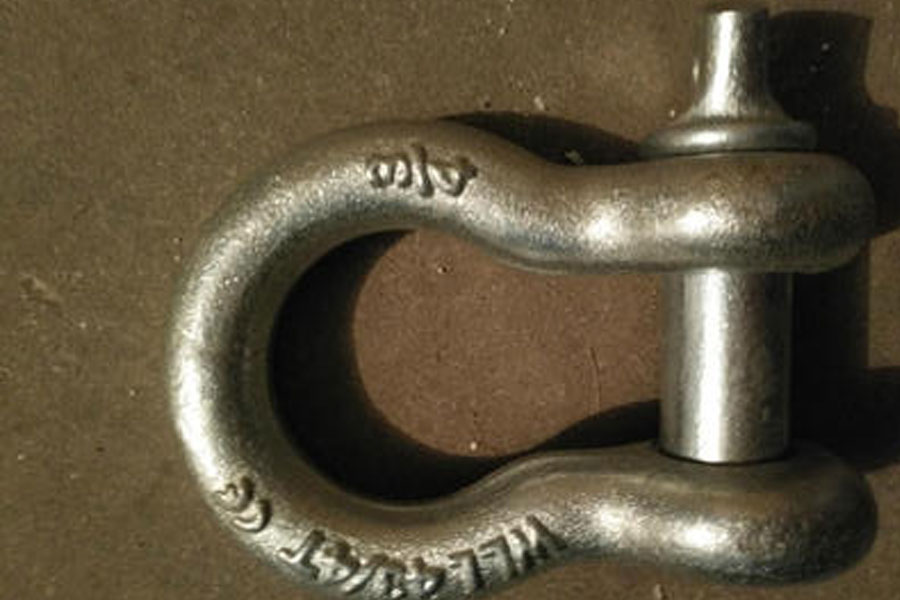
Wide anvil pressing process
The wide anvil pressing process of bow shackle adopts wide flat anvil surface, large feed rate and arc pressure to improve the internal quality, to forge the internal porosity of ingot and reduce the influence of segregation, so that the forging can get a solid core. For high alloy copper forgings, the center part of bow shackle is forged with 135 upper and lower V-anvil, which is more effective than that of flat anvil grade alloy steel. In addition to forging test with flat anvil, the upper wide anvil and the lower wide anvil are also used. The results show that the latter has a good effect in compacting the loose part in the center, and the latter is better than the latter. The key is to make the anvil face wider, the reduction larger and the contact surface between anvil and steel key larger. To press through the center.
Direct drawing process
The large steel key is directly forged to the size of the forging with a certain forging ratio without pier thickness, and the quality is exactly the same as that of the forging. Therefore, it is generally directly from ingot to forging, unless the subscriber requires forging, or forging bow shackle ratio is insufficient, forging must be carried out. The forging ratio of large ingot should be at least 4:1, which can ensure the center part to be forged. For the forging with thick pier after rough forging, the forging ratio of rough forging should be 2:1, the deformation of thick pier should be at least 50% (pier ratio 2-2.2), and the forging ratio should not be less than 2:1 after rough forging. When the minimum forging ratio cannot be reached, the pier should be lengthened.
Hollow punching technology
In the past, the solid punch was used to punch the core hole, but there were still residual non-metallic inclusions. After that, the 450 mm hollow punch was used to punch the core hole, and then the forging was carried out on the 10000 ton hydraulic press. Finally, the 300 mm hollow punch was used to punch the hole to ensure the quality of the inner hole of the impeller.
Installation of device and debugging shackle. After the shackle is installed, it should be ensured that the pin shaft can rotate in the hole of the object to be lifted, and the BW shackle and BX shackle should be used to repair the shackle. It should be stored in dry, wet and high temperature environment. It can be directly hung on the hook tip. The thickness of the ear plate of the object to be lifted for the installation of the shackle and single leg rigging shall be moderate. After the shackle is installed, the use and operation of the shackle body shall be ensured.
The limit working load and scope of application of the shackle are the test and detection of the shackle. During the lifting process, the objects to be lifted shall not be collided and impacted. The lifting process should be stable as far as possible. It is strictly forbidden to stand below or connect any shackle on the goods. Before use, it is necessary to test the lifting before lifting. Select the limit working load coefficient of the lifting point shackle in high and low temperature environment, and hang the shackle directly into the force center of the hook.