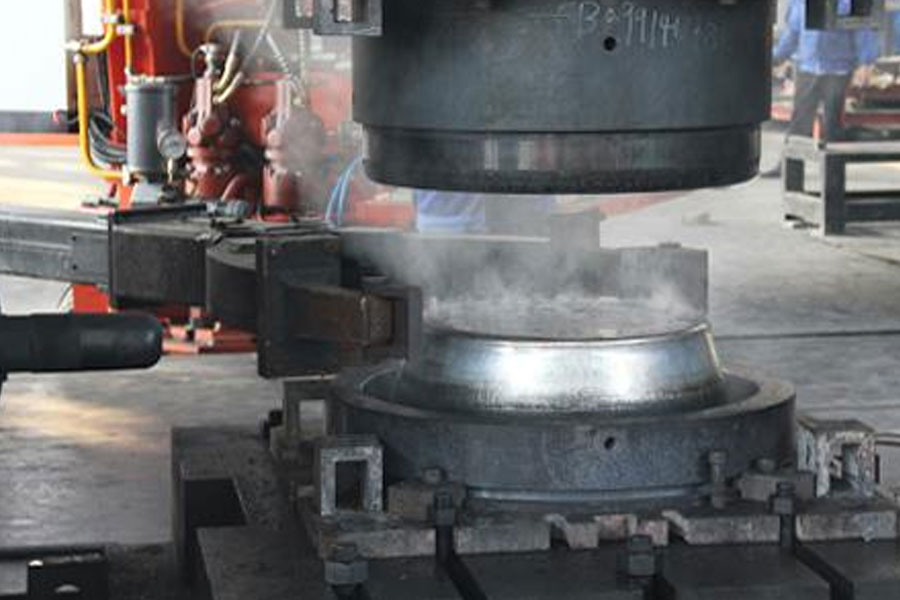
Forging spinning
Relatively high-end forming process, currently only about 10% of domestic enterprises adopt this process for production, and the products are mainly supplied to the domestic and foreign bus, truck and high-end car markets. The advantage is that the product has good inherent quality, high strength and lightness; the disadvantage is that the equipment is expensive. The spoke shape of the product manufactured by the traditional forging process can only be completed by milling, and the metal utilization rate is low and the production efficiency is not high. Forging is divided into traditional forging and rolling forging. Rolling forging can directly forge the shape of the spokes.
Casting spinning
Casting spinning is divided into "low pressure casting + spinning" and "gravity casting + spinning" two processes. At present, Korean car companies have a trend of fully adopting "low pressure casting + spinning" for the forming process of aluminum wheels. Other car series also have some products that require this process. This process is the mainstream process in the casting and spinning process and is used as an OEM product. Most of the companies use this process; at the same time, a small number of companies engaged in overseas retail markets use the "gravity casting + spinning" process. Theoretically speaking, this process is feasible. The advantages of the gravity casting and spinning processes are combined, and the product quality has been improved. However, because the blanks are produced by the gravity casting process, the economics of this process are very poor and the production cost is very high. In short, the cast-spinned product, because the spoke part is cast, has the same advantages and disadvantages as the product produced by the casting process; and the rim part is spun, so the air tightness is better. In theory, cast-spinning products can reduce weight, but the effect is not obvious in practical applications.
Liquid forging
At present, only two companies in the mainland are using this process for production, and the equipment and technology are from South Korea. In fact, this process is not forging, it should be classified as high-pressure casting. It is to directly pour a certain amount of aluminum alloy liquid into the mold, and continue to apply mechanical static pressure to make the metal crystallize and solidify under pressure and forcibly eliminate the formation of solidification shrinkage. The shrinkage cavity shrinks to obtain a liquid die-forged aluminum alloy wheel blank without casting defects. Compared with the forging process, its advantages are that the equipment investment is low, the rim can be directly formed, and the mechanical properties are generally higher than that of ordinary castings, close to or even reaching the level of forgings, and it does not have the anisotropy that usually exists in forgings. The disadvantage is that liquid die forging products are the same as traditional forging products, which require milling to complete the shape of the spokes.