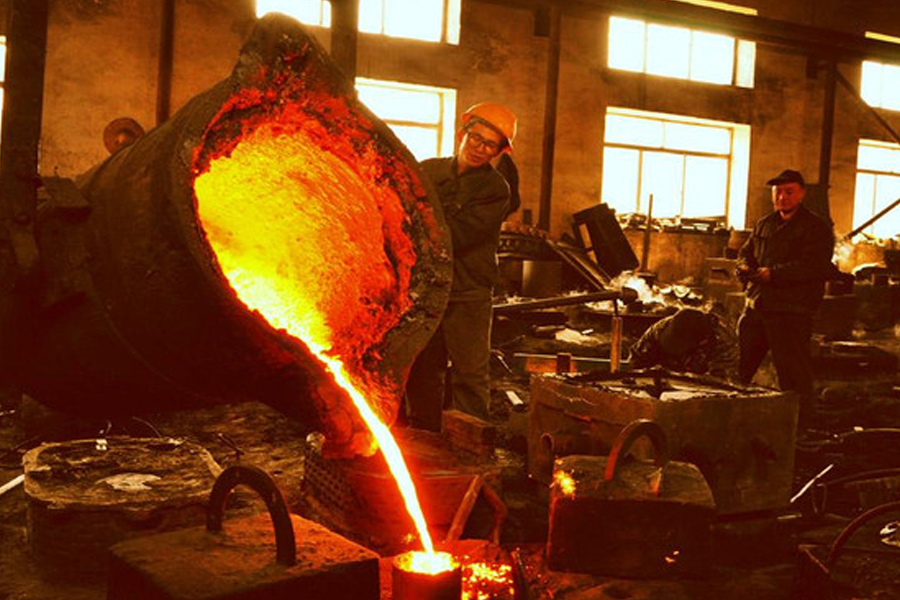
Composition of investment casting process cost
The process of all silica sol investment casting can be divided into four stages: wax mold manufacturing, shell making, melting and pouring, and post-treatment. The cost of inspection and equipment maintenance for these four stages is classified as auxiliary production cost. In the four production processes, the cost in the three stages of wax mold manufacturing, shell making, melting and pouring is closely related to the process yield. It is more accurate to calculate the cost by pouring weight than by casting weight directly.
For example, if the wax mold manufacturing cost is calculated according to the casting weight, the cost relationship between small and large parts is obviously not in line with the reality. Therefore, the more reasonable method is that the cost of wax mold manufacturing, shell making, melting and pouring process (referred to as the front section cost in this paper) is calculated according to the weight of molten steel pouring (referred to as the pouring weight in this paper), and the cost of post-treatment and auxiliary production (referred to as the back section cost in this paper) is calculated according to the weight of casting. The manufacturing cost and its composition calculated according to the weight of molten steel and casting are shown in Table 1, and the proportion of its distribution structure is shown in Figure 1 and Figure 2. It can be seen that the cost of shell making and smelting phase accounts for more than 60% of the process cost.
Main factors affecting cost difference of investment castings
Strictly speaking, the manufacturing cost of different castings in each process is not exactly the same, but the difference in some links is very small, which can be calculated according to the average level. We should pay attention to the factors that have a greater impact on the casting cost. The main factors leading to the difference of casting process cost are as follows:
1. Process yield
Process yield, also known as yield, is the percentage of the actual casting weight in the pouring weight. For a specific casting, the process yield is equal to the percentage of the total casting weight in the same tree. It is related to the casting structure and group plan. It may vary from 30% to 60%, generally between 40-50%. The relationship between the former cost and the process yield is as follows
The former cost per kilogram of casting is inversely proportional to the process yield. The lower the process yield is, the higher the former cost per unit weight of casting is, and the lower the process yield is, the more significant the influence is. The first stage cost of pouring molten steel per kilogram is 6 yuan. When the process yield is 45%, the first stage cost of casting per kilogram is 13.33 yuan; When the process yield is 30%, the front cost of casting is 20 yuan / kg, which is 6.7 yuan higher than the average level, and the process cost increases by 37.6%. The influence on the total cost of 304 stainless steel casting is about 17%; When the process yield is 60%, the front cost of casting is 10 yuan / kg, which is 3.3 yuan lower than the average level, and the process cost is reduced by 18.5%. For 304 stainless steel casting, the total cost is reduced by about 7%;
When the process yield is 45%, the front cost per kilogram of casting will increase by 0.3 yuan per percentage point, and when the process yield is 30%, For each percentage point reduction, the front cost per kilogram of castings will increase by about 0.67 yuan
It can be seen that the effect of process yield on cost is very significant. Like the power factor in Electrotechnics, reducing the process yield is equivalent to increasing the reactive power consumption. Of course, the higher the process yield is, the better it is, and it is not high to want to be. Too high process yield will reduce the feeding capacity of the gating system, resulting in insufficient feeding and shrinkage porosity or shrinkage defects; On the other hand, some castings, especially thin-walled castings with irregular shape, are difficult to improve the process yield due to the limitation of casting structure and group plan. This important factor should be considered when determining the casting price.
2. Shell layers
Due to the different shape and structure of castings, the number of shell layers will be different. For example, castings with long and thin holes or slots need to be faced twice or even three times; Generally, two backing layers are enough for castings, while three or more backing layers may be required for larger castings. The cost of shell making per kilogram of casting is about 5.9 yuan, of which 67.8% is material cost, 23.9% is fuel and power cost, and 13.3% is salary cost. Among the 4 yuan / kg shell material cost, the consumption of zirconium sand and zirconium powder accounts for about 63%, 42.7% of the whole shell cost, and the cost of silica sol accounts for about 12.2% of the shell cost. Although zirconium sand zirconium powder is only used for surface shell making, it becomes the main item of shell making cost because of its high price.
It can be seen from the table that the cost of the surface layer is about 4.4 times that of the back layer. Moreover, the materials used for the second surface course are more than those used for the first one. According to an increase of 10%, the cost of making an additional surface course is about 6.2 yuan. The average cost per kilogram of casting is increased by 2.7 yuan, and the cost per kilogram of pouring weight is increased by 1.21 yuan. That is to say, the shell making cost per kilogram of casting increases by 45.8% and the process cost per kilogram of casting increases by 15.1%. For 304 stainless steel, the impact on the total cost and price is about 7%. The cost per kilogram of casting increased by 0.56 yuan, and the cost per kilogram of pouring weight increased by 0.25 yuan. The shell making cost per kilogram of casting increases by 9.4%, the process cost per kilogram of casting increases by 3.1%, and the impact on the total cost of 304 casting is only about 1.4%.
2.Difficulty of post-processing
After casting pouring, the qualified castings can only be obtained through the post-treatment processes such as shell crushing and sand cleaning, cutting, grinding, shot blasting, pickling, shaping, repair welding and repair. The average cost of post-treatment can be determined according to the weight of castings. As shown in Table 1, the average cost of post-treatment per kilogram of castings is 3.33 yuan.
The cost of pickling for stainless steel castings is about 0.3 yuan / kg. Although the carbon steel parts do not need pickling, considering that the box needs to be buckled after pouring, and it is difficult to remove sand after bucking, and the finished products need rust prevention and other factors, the cost difference can not be distinguished.
When the structure of castings is different, the process content and difficulty of post-treatment are also different. Generally, after casting, the process of shell crushing, cutting, grinding, shot blasting and so on is OK, while some castings need to increase the process. When the customer requests to add heat treatment, surface treatment, machining and other work content to the casting blank, the cost should be accounted separately and included in the total price, which is not within the scope of this paper. The cost difference of post-treatment mainly comes from sand cleaning, deformation correction and renovation. The cost depends on the casting structure and technical requirements. The cost difference should be considered when determining the price.
Apportionment of administrative expenses
Enterprise management fee is an integral part of the sales cost of product factory, which can be apportioned to specific castings by weight. The pre evaluation of quotation can first determine an expected breakeven Output or average output, and then calculate the management cost per kilogram of castings according to this output. The post evaluation should be distributed according to the actual amount. Management fee is related to enterprise scale and product structure. Factories with simple and stable product structure need lower management fee, while enterprises with more varieties and high technology content need higher management fee. The management fee level of medium-sized hardware investment casting factory is about 5 yuan per kilogram of castings.
Cost accounting model of investment castings
1. Average product per kg of casting
According to the above method, the process cost and factory cost (yuan / kg) per kg of 304 stainless steel conventional casting with different process yield and different shell making scheme are calculated
2. Single casting cost
Casting in the production process, regardless of size, should be carried out one by one according to the specified process. Therefore, the actual cost of the casting is not completely proportional to its weight, especially for very small castings, the cost deviation calculated by weight is large. We calculate the casting unit cost according to the weighted average of the average kilogram cost and the unit cost by 9:1. Expressed as
Supplementary process cost refers to the cost of sand cleaning (such as sand drilling, acid biting, sand blasting, alkali blasting, etc.) and shaping and other additional processes. The cost of heat treatment, surface treatment, welding and machining outside the casting process should be calculated separately, which is not in the scope of this paper.
The Price evaluation of castings
After the cost of the casting is clear, the evaluation of the price of the casting is easy. Casting price evaluation is divided into pre-evaluation and post-evaluation. The purpose of pre-assessment is to quote, and the purpose of post-assessment is to analyze profit and loss. There are unknown factors in the pre-assessment. The standard cost can be estimated based on the statistical analysis of historical data. During the post-assessment, the various expenses are known, and the expenses can be collected according to the specific product. The allocation of expenses should be as consistent as possible with the actual situation.
The basis of casting price evaluation is the cost of sales of the factory, in addition to the expected profit, sales tax, sales expenses, etc. Expressed by the formula as
Casting price = factory sales cost + expected profit + sales tax + sales expense
Among them, there are many factors that need to be considered in determining the expected profit, and the range of change is also relatively large, generally around 15%. In summary, the main factors that need to be considered for expected profits are as follows:
Postscript: It should be pointed out that the purpose of this article is to explore the factors affecting the cost of investment castings and to scientifically evaluate the cost of investment castings. Since the actual cost levels of various investment casting plants are not the same, the statistics cited in this article are for reference only. The cost collection method adopted in this article is not completely consistent with the conventional industrial accounting practices, and needs to be identified when data collection.