Aluminum alloy wheels have many characteristics that steel wheels cannot match. Therefore, aluminum alloy wheels have been widely used in cars, motorcycles and other vehicles. By 2002, the loading rate of aluminum alloy wheels for cars in China was close to 45%. Due to the high quality requirements of automobile wheels, its structure is suitable for low-pressure precision casting, and the demand is large, it has greatly promoted the development of low-pressure casting technology. At present, low-pressure casting has become the main process method for the production of aluminum alloy wheels, and most of China's aluminum alloy wheel manufacturers use this process for production.
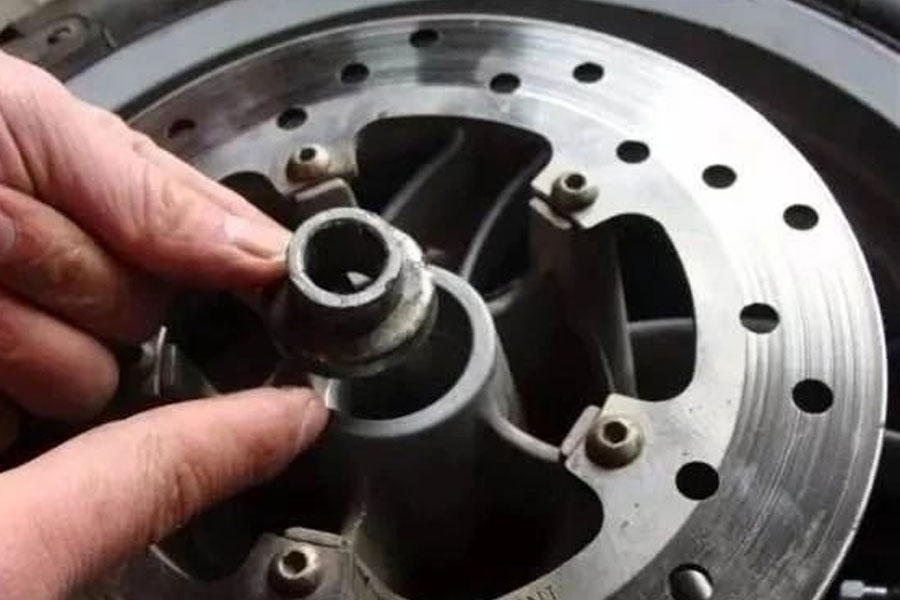
The cracks of the low-pressure precision casting aluminum alloy wheel hub are mainly caused by the stress concentration, or the crack caused by uneven force when the hub is ejected, or the liquid solidification at the riser pipe. Cracks are generally divided into cold cracks and hot cracks. Cold cracking refers to the cracks formed when the alloy is below its solidus temperature. In layman's terms, cold cracking is caused when the precision casting stress acting on the casting exceeds the degree allowed by the strength or plasticity of the casting itself when the precision casting is cooled to a low temperature. Cold cracks mostly appear on the surface of castings, with slight oxidation on the surface of the cracks; while hot cracks are usually considered to be generated during the solidification of the alloy. Due to the heat transfer of the mold wall, the castings always start to solidify from the surface. When a large number of branches appear on the surface of the casting and overlap to form a complete skeleton, the casting will appear solid state shrinkage (often expressed as linear shrinkage).
However, there is still a layer of liquid metal film (liquid film) between the dendrites at this time. If the shrinkage of the casting is not hindered, the dendrite layer is not affected by force and can shrink freely, and it will not appear. stress. When the shrinkage of the dendrite layer is hindered, it cannot shrink freely or is under the action of tensile force, and tensile stress will appear. At this time, the liquid film between the dendrites will be deformed by stretching.
When the tensile stress exceeds the strength limit of the liquid film, the dendrites will be pulled apart. However, there is still some liquid metal around the cracked part. If the liquid film is pulled apart very slowly and there is enough liquid around and flows into the cracked part in time, the cracked part will be filled and "healed". Precision casting products will not show hot cracks. If the tensile cracks cannot be "healed" again, hot cracks will appear in the precision casting products. The surface of the thermal fracture is strongly oxidized, showing a dark or black color with no metallic luster.