The Causes Of Cracks
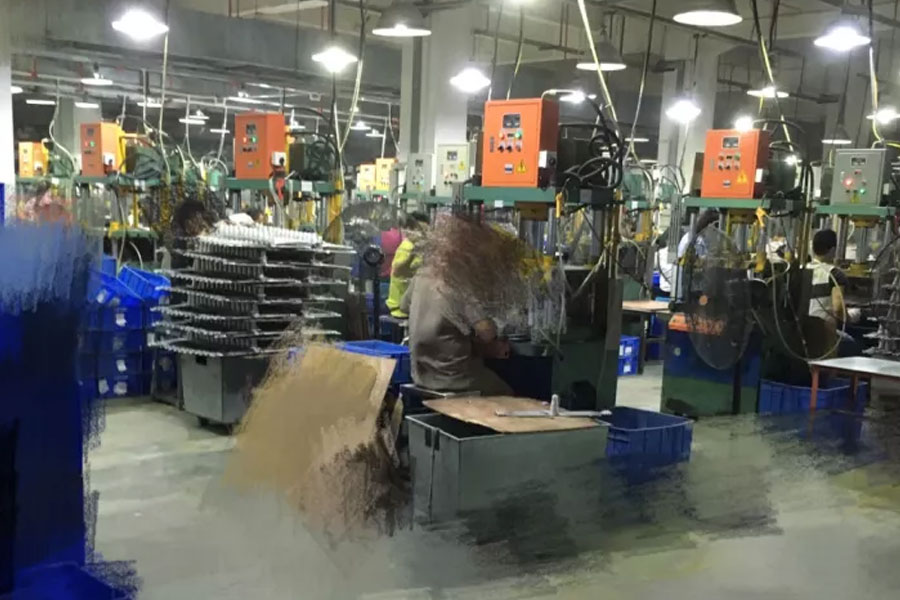
Early cracking is generally due to the high forging temperature of the blank forging (commonly known as overburning). Overburning is an irremediable defect, so the forging temperature during the blank manufacturing process should be strictly controlled. The same is true for the quenching process. The heating time should be strictly controlled to prevent decarburization. After the material is selected, it is heat treatment. After a certain amount of production, pay attention to stress relief. Also, the design should be reasonable, try to avoid stress concentration, and pay attention to the size of the R angle. At about 10,000 mold times, the mold should pay attention to tempering to remove the stress. The residual stress of the internal force concentrated processing is not removed. The thermal stress of the die-casting process is not well removed. In short, the crack is the performance of stress concentration. You can use multiple tempering to remove the stress. Can increase mold life.
The main reasons for the cracking of aluminum alloy die-casting molds after a period of production are as follows:
To prevent the die-casting mold from cracking and increase the service life of the mold, the following points must be done:
The specific specifications are as follows:
After the new mold is produced for a period of time, the accumulation of thermal stress is the direct cause of the mold core cracking. In order to reduce the thermal stress, the mold core and slider after a certain period of time should be tempered to eliminate thermal stress.The specific production modes that need to eliminate thermal stress are as follows:
The aluminum alloy die-casting mold bears huge alternating working stress, and attention must be paid to the mold material, design, processing, heat treatment and operation in order to obtain a long mold life. The following are 25 tips for making the mold achieve a long life: