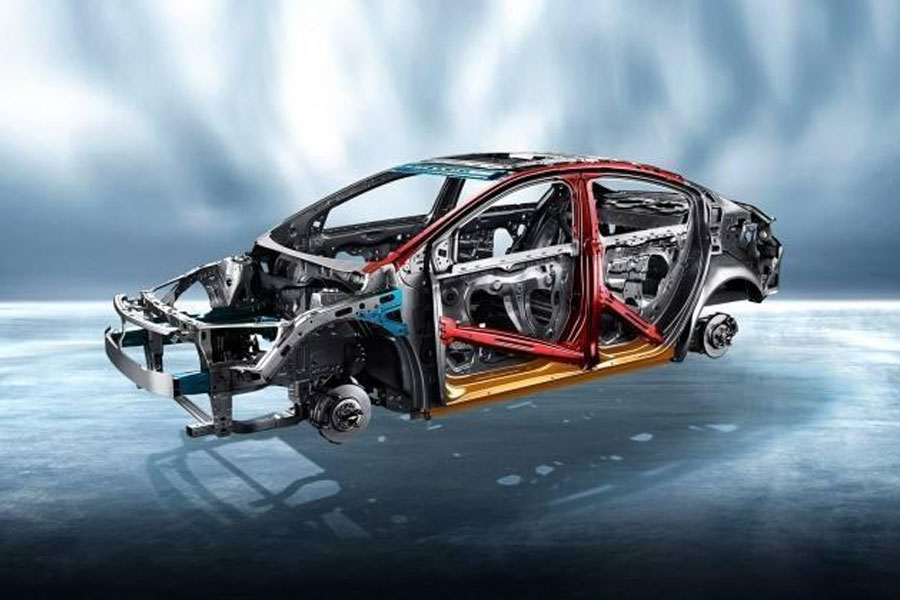
The benefits brought by the increase in the amount of automotive aluminum are mainly reflected in the following aspects:
Typical applications of aluminum alloy castings in automobiles
Structural parts and covering parts are made of aluminum plate stamping parts, which are more than 100 kilograms lighter than similar cars. The aluminum alloy for structural parts has good axial shrinkage and excellent energy absorption, which is beneficial to improve safety.
The metal mold gravity casting process is characterized by pouring liquid metal into the metal mold by gravity pouring to form castings. The quality of the castings is better than that of aluminum alloy sand casting. It is a traditional method for producing higher quality castings. The Ford Motor Company of the United States built an aluminum casting plant in Brood Park Ohio in 1998 at a cost of $99 million. It uses a metal mold gravity casting method to produce aluminum cylinder blocks and aluminum cylinder heads. In addition, General Motors of the United States also uses the metal mold gravity casting method to produce V8 aluminum cylinder blocks. Metal mold low pressure casting is a process between metal mold casting and die casting. The aluminum melt fills the cavity from one or two gates located at the bottom along the riser tube under pressure, and moves away from the gate. The place starts to solidify and gradually expands toward the gate.
The utilization rate of aluminum melt in low pressure casting is much higher than that of metal mold casting, reaching 85% ~ 90%, while metal mold casting is only 40% ~ 60%, and the product has higher mechanical properties and better compactness. , But its scrap rate is relatively high, and the production process is also more complicated.
Related Pages:AUTOMOTIVE PARTS
Related Product: