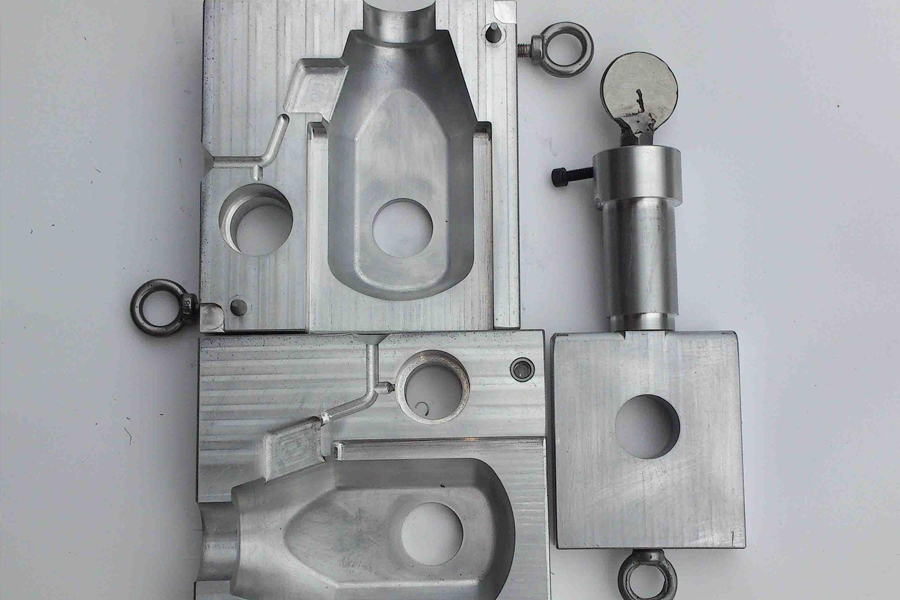
One of the most important issues for the development of 700 ℃ steam temperature A-USC generator sets is the development of heat-resistant alloys for turbine impellers. Some researchers have developed Ni-0.05C-18Cr-13Co-9Mo-1.3Al-1.4Ti-0.1Ta-0.3Nb alloy based on Inconel 617 as the basic material and improved the alloy composition, and trial-produced A large-scale forged impeller sample that simulates the impeller of a real machine. There are research reports on the material properties of different parts of the impeller sample.
Evaluated the casting alternative materials that can be applied to A-USC generator sets with a steam temperature of 700℃. Regarding the Ni-0.04C-26Cr-21Co-1Al-1.9Ti-1.8Nb alloy, trial-produced castings with 3-layer stepped wall thicknesses were made and the materials were evaluated. A research report introduced the influence of segregation on creep strength.
Ni-Fe-based superalloy is expected to be the material of turbine impellers for A-USC thermal power generation. However, in order to ensure the characteristics and manufacturability of turbine impellers, it is important to control trace elements. There are still many unclear points about the influence of trace elements in Ni-Fe-based superalloys parts for turbine impellers. Therefore, some researchers have investigated the influence of trace elements in terms of creep characteristics.
In the process of developing 700℃-class A-USC generator set, in order to apply different material welded impellers composed of Ni-based and Fe-based impellers into practice, the structural stability and mechanical properties of the impeller welded part at high temperature were proposed. Claim. Some researchers have produced a low-alloy steel/Inconel 617 welding material as the interface style of different Fe/Ni materials, and evaluated the effect of thermal aging on the microstructure change of the welding interface.
In order to reduce CO2 emissions, extensive research has been conducted on A-USC equipment. 23Cr-45Ni-7W alloy (ASTM UNS N06674) is a material that improves the creep strength by strengthening the precipitation of M23C6 and Laves phases. It can be used as an alternative material for A-USC's high-temperature steam tubes and boiler tubes. Some researchers evaluated the influence of the alloy's creep characteristics on the Laves phase precipitation behavior.
In order to develop A-USC generator sets with a steam temperature of 700℃, the possibility of using Ni-based heat-resistant alloys as boiler parts was studied, and it was pointed out that alloy 617, which is a precipitation-strengthened alloy, has relaxation in the process of high-temperature use. Cracks (SR cracks) and other related issues. On the other hand, the 23Cr-45Ni-7W alloy (ASME-CC2684), which does not use the phase as the precipitation strengthening phase, has a slightly lower creep rupture strength at 700°C than that of the alloy 617, while the 30Cr-50Ni-W alloy has not been precipitated. It is strengthened, but the creep rupture strength is higher than that of 23Cr-45Ni-7W alloy. Its ductility and SR crack resistance are good. It can be used for A-USC main steam pipe. A research report introduced the four types of structures, mechanical properties and creep characteristics of the plates and trial-produced large-diameter pipes.
At present, the energy problem has become a very important issue. In order to improve the efficiency of thermal power generation as the main power supply means, extensive research and development have been carried out on forged Ni-based alloys. For the stability of the Ni-based superalloy's strengthening phase, the phase structure, not only the precipitation behavior of the phase will have an important effect, but also the morphological change caused by the lattice mismatch between it and the parent phase. Have an important impact. However, the research on these microstructures is mainly the research on the cast Ni-based superalloys with high phase volume ratio, while the research on the cast alloys is very few. Therefore, some research reports have investigated the relationship between the change of the phase structure and the lattice misalignment in the forged Ni-based alloy.