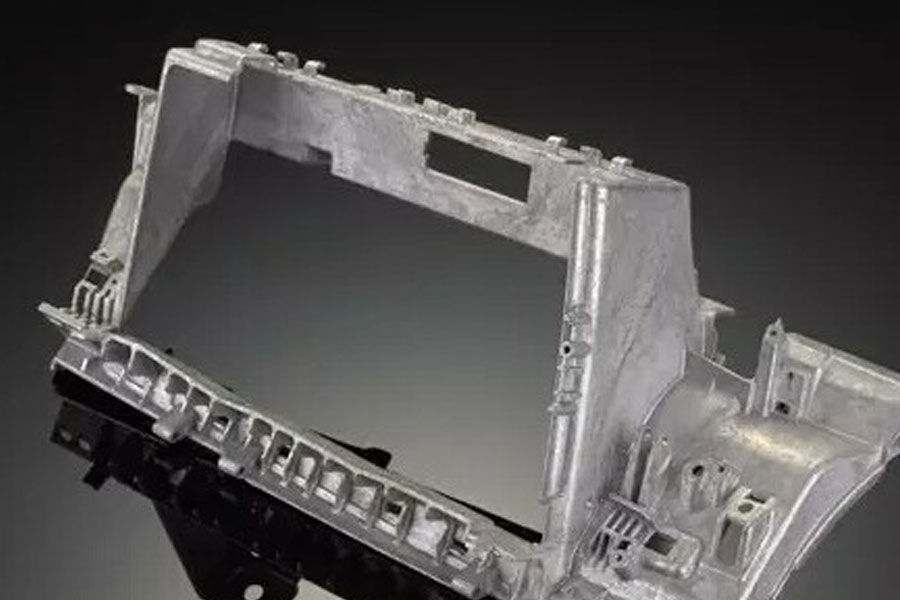
Due to its high production efficiency, low cost, and the ability to produce products with more complex shapes, the casting molding process has a good liquid filling ability and occupies a dominant position in the magnesium alloy molding method. However, due to the production process of cast magnesium alloys, the structure is not dense enough, and there are many defects such as shrinkage porosity and shrinkage cavity, and the mechanical properties are poor. Magnesium alloy products manufactured through plastic machining processes such as extrusion, forging, rolling, etc., have a denser structure and can well improve the mechanical properties of magnesium alloy products. At present, due to the lack of efficient and low-cost magnesium alloy plastic machining methods, the application of magnesium alloy plastic machining is limited. Therefore, the development of high-efficiency and low-cost magnesium alloy plastic machining methods has become the only way to promote the large-scale application of high-strength magnesium alloys. Magnesium alloys mainly have the following plastic machining techniques:
Forged
The forging process of magnesium alloys is more complicated. During the forging process, local deformation is prone to unevenness, so that the properties and structure of the workpiece will also be uneven. Mg-Zn-Zr series and Mg-Al-Zn series are commonly used forged magnesium alloys. When there are higher requirements for the strength of materials at higher temperatures, the strength of magnesium alloys with rare earth elements added to the WE series can easily meet the requirements. During the forging process, the degree of deformation, the final forging temperature, and the way of deformation are the main factors affecting the mechanical properties of magnesium alloy forgings. At present, it has mainly developed forming technologies such as punch forging, isothermal forging, and warm precision forging.
Extrusion Molding
Extrusion molding is a plastic machining method in which a metal blank to be formed is placed in a closed extrusion cylinder and a certain pressure is applied to the blank to deform the material in the extrusion die. Since the metal blank is in a three-dimensional compressive stress state during the forming process, the plasticity of the metal blank can be fully exerted in the forming method. Extruded products have good surface quality, high dimensional accuracy, and compact structure. Therefore, magnesium alloy extrusion products are in large demand in the automotive, aerospace, and electronics fields. Generally, the extrusion of magnesium alloy can be divided into hot extrusion and warm extrusion, and the equipment used is basically the same as that of other metal materials.
Roll Forming
Magnesium alloy sheet has broad application prospects in the aerospace and automotive 3C industries due to its unique advantages. Most of the magnesium alloy sheets currently in use are formed by rolling. However, the rolling forming process of magnesium alloy sheet is more complicated, and usually requires 3 or more passes of hot rolling. Magnesium alloy sheet rolling has the following characteristics: low yield, low production efficiency, large profits, and relatively single varieties.
Stamping And Forming
The stamping process of magnesium alloys is different from other materials. Magnesium alloys have low plasticity at room temperature. Conventional cold stamping forming is not suitable for magnesium alloys. Magnesium alloys usually need to be heated to 150°C or higher to perform hot stamping forming. At present, the hot stamping of magnesium alloys has been studied to a certain extent, but its key problems have not been well solved, which to a certain extent hinders the wide application of magnesium alloy sheets in industry.
Draw Forming
In the process of drawing and forming of magnesium alloy, the material is in a state of stress under tension and compression in both directions. At this time, the plasticity of the material is difficult to exert. Therefore, drawing is not suitable for the forming of magnesium alloy. The drawn products have the characteristics of high surface roughness and good dimensional accuracy. Wire and pipe are produced by drawing and forming process, which has high production efficiency and is easy to realize high-speed and continuous production. And the strength of the magnesium alloy wire formed by drawing is higher.
Superplastic Forming
The superplastic forming process can be used to process workpieces with complex shapes and large deformations. It is a metal characteristic that exceeds the general plasticity index under certain conditions. Therefore, superplastic forming can be used to process magnesium alloy products with poor plasticity. However, since the research on superplastic forming of magnesium alloys has just started, there are many problems. It is difficult to reach a consensus on the superplastic deformation mechanism of magnesium alloys. The superplastic forming of magnesium alloys needs further research.